Pharmaceutical Industry Courses (Online)
Retrain or upskill for a new career or promotion in biopharmaceutical manufacturing, pharmaceutical manufacturing, medical device manufacturing, quality assurance (QA) and GMP, quality control (QC), equipment qualification, CQV, C&Q, process validation, CSV, risk management.
Start Here↓
Answer 4 questions to get a personalised course recommendation. Or scroll down to explore all courses.
Conversion Course into Pharmaceutical Manufacturing
Ideal for:
- People from all backgrounds wanting to retrain for a new career in pharmaceutical manufacturing
Duration: 10 weeks
Hours per week: 12
Awarding body: GetReskilled
University Certificate in eBioPharmaChem (Level 7)
🏆 Winner of Best Online Learning Experience – Irish Education Awards
🎓 University Accredited by TU Dublin, Ireland | Level 7 | 15 ECTS credits
Ideal for:
- Those with pharmaceutical or med device manufacturing experience
…who want: to move into more senior manufacturing roles or have their knowledge recognized in a university accredited certificate
Duration: 37 weeks
Hours per week: 14 hrs
The ideal choice for mature students
Ideal for:
- UK residents of all backgrounds
…who want: to move into more into pharmaceutical and medical device manufacturing roles with a university-accredited degree
Duration: 4 years
Hours per week: 14 hrs
Awarding body: University of South Wales
Conversion Course into Pharmaceutical Manufacturing
Ideal for:
- All backgrounds
…who want: to retrain for a new career in pharmaceutical manufacturing
Duration: 10 weeks
Hours per week: 12
Awarding body: GetReskilled
Equipment Validation Training Course For Starter Validation, CQV and C&Q Roles
Learn how to populate a 120-page plus IQ OQ PQ Protocol and qualify equipment and systems
Ideal for:
- Those with Commissioning & Qualification experience in ANY industry
OR - Engineers, mechanical contractors, quality specialists, pipefitters, plumbers, pipe welders, instrument or boiler technicians (i.e., those who can interpret technical drawings)
OR - Those with GMP manufacturing experience
…who want: a starter-level validation, CQV or C&Q role in equipment validation with a pharmaceutical company, engineering consultancy or engineering contractor.
Duration: 15 weeks
Hours per week: 15
Awarding body: GetReskilled
Pharmaceutical Validation Training Course Advance to More Senior Validation, CQV and C&Q Roles
University Certificate in Validation (Level 7)
🎓 Accredited by TU Dublin, Ireland | Level 7 | 15 ECTS credits
Ideal for:
- Those with a sound understanding of GMP rules and regulations
AND - Can read engineering documentation such as P&IDs and piping isometrics
AND - Can populate an IQ OQ PQ equipment validation protocol
…who want: more senior level validation, CQV and C&Q roles in pharmaceutical manufacturing
Duration: 30 weeks
Hours per week: 14
Extend Your Role to Computer System Validation (CSV) Projects. Get Certified and Become a CSV Professional
Ideal for:
- Anyone with an understanding of GMP rules and regulations
AND you are any of the following…
- Validation Engineer/Specialist or Senior Validation Manager
- PhD, Masters or Degree in Biochemistry, Microbiology, Molecular Biology, Lab/Science, etc
- Automation, Control/Instrumentation, Process, Manufacturing, etc Engineer or Technician
- Quality Assurance or Quality Control Technician or Specialist
- Metrology, Maintenance Engineer, Technician or Specialist
- Front/Backend Developer
…who want: to manage electronic data in a regulated manufacturing/laboratory/clinical environment in compliance with FDA’s 21 CFR Part 11 or other regulatory guidelines using the GAMP framework
Duration: 10 weeks
Hours per week: 12
Awarding body: GetReskilled
Equipment Validation Training Course For Starter Validation, CQV and C&Q Roles
Learn how to populate a 120-page plus IQ OQ PQ Protocol and qualify equipment and systems
Ideal for:
- Those with Commissioning & Qualification experience in ANY industry
OR - Engineers, mechanical contractors, quality specialists, pipefitters, plumbers, pipe welders, instrument or boiler technicians (i.e., those who can interpret technical drawings)
OR - Those with GMP manufacturing experience
…who want: a starter-level validation, CQV or C&Q role in equipment validation with a pharmaceutical company, engineering consultancy or engineering contractor.
Duration: 15 weeks
Hours per week: 15
Awarding body: GetReskilled
Extend Your Role to Computer System Validation (CSV) Projects. Get Certified and Become a CSV Professional
Ideal for:
- Anyone with an understanding of GMP rules and regulations
AND you are any of the following…
- Validation Engineer/Specialist or Senior Validation Manager
- PhD, Masters or Degree in Biochemistry, Microbiology, Molecular Biology, Lab/Science, etc
- Automation, Control/Instrumentation, Process, Manufacturing, etc Engineer or Technician
- Quality Assurance or Quality Control Technician or Specialist
- Metrology, Maintenance Engineer, Technician or Specialist
- Front/Backend Developer
…who want: to manage electronic data in a regulated manufacturing/laboratory/clinical environment in compliance with FDA’s 21 CFR Part 11 or other regulatory guidelines using the GAMP framework
Duration: 10 weeks
Hours per week: 12
Awarding body: GetReskilled
Need help? Chat with an expert to find out the best course to take
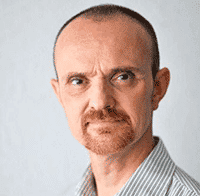
Hi, I’m Donagh Fitzgerald. I’ve spent over 14 years helping people figure out what kinds of jobs they can get in the pharmaceutical and medical device manufacturing industry based on their work experience.
Have a question? You can chat with me live any time – just click the blue chat bubble in the bottom-right corner of the page.
I’m online Monday to Friday during working hours (Irish/UK time).
If I’m away from my desk, just leave a message and I’ll get back to you as soon as I can.
GMP Training Course for the Pharmaceutical Industry For Individuals, Teams, Companies or Startups
Learn GMPs, the specialised terms and frameworks used so you can work better with your clients in the pharmaceutical industry
Ideal for:
- All backgrounds
…who want: to get a deep understanding of Good Manufacturing Practices (GMPs) really fast.
Duration: 6 weeks
Hours per week: 10
Awarding body: GetReskilled
Conversion Course into Pharmaceutical Manufacturing
Ideal for:
- All backgrounds
…who want: to retrain for a new career in pharmaceutical manufacturing
Duration: 10 weeks
Hours per week: 12
Awarding body: GetReskilled
University Certificate in eBioPharmaChem (Level 7)
🏆 Winner of Best Online Learning Experience – Irish Education Awards
🎓 University Accredited by TU Dublin, Ireland | Level 7 | 15 ECTS credits
Ideal for:
- Those with pharmaceutical or med device manufacturing experience
…who want: to move into more senior manufacturing roles or have their knowledge recognized in a university accredited certificate
Duration: 37 weeks
Hours per week: 14 hrs
GMP Training Course for the Pharmaceutical Industry For Individuals, Teams, Companies or Startups
Learn GMPs, the specialised terms and frameworks used so you can work better with your clients in the pharmaceutical industry
Ideal for:
- All backgrounds
…who want: to get a deep understanding of Good Manufacturing Practices (GMPs) really fast.
Duration: 6 weeks
Hours per week: 10
Awarding body: GetReskilled
Conversion Course into Pharma for Scientists
Ideal for:
- anyone with a PhD, Masters, or Degree in lab/science, biochemistry, molecular biology, chemistry, microbiology or biotechnology
…who want: to work in Quality Control, Quality Assurance roles or science roles in development or that support manufacturing in the pharmaceutical manufacturing industry
Duration: 15 weeks
Hours per week: 14
Awarding body: GetReskilled
Conversion Course into Quality Roles in Pharma
Ideal for:
- anyone with a PhD, Masters, or Degree in food science, pharmacy or pharmacology or a quality control or quality assurance background
…who want: to work in a quality control, quality assurance or lab role in the pharmaceutical manufacturing industry
Duration: 15 weeks
Hours per week: 14
Awarding body: GetReskilled
Conversion Course into Engineering Roles in Pharma
Ideal for:
- anyone with a PhD, Masters, Degree, or Diploma in mechanical, facilities, production, maintenance, manufacturing, industrial, quality, plant, maintenance, or civil engineering background
…who want: to work in the same or similar kinds of roles within the pharma and medical device industry or engineering consultancies
Duration: 18 weeks
Hours per week: 14
Awarding body: GetReskilled
Conversion Course into Clean Utilities Roles in Pharma
Ideal for:
- anyone with a PhD, Masters, Degree, or Diploma in mechanical, facilities, production, maintenance, manufacturing, industrial, quality, plant, maintenance, or civil engineering background
…who want: to work in the same or similar kinds of roles within the pharma and medical device industry or engineering consultancies
Duration: 18 weeks
Hours per week: 14
Awarding body: GetReskilled
Fill in your regulatory, risk management, and validation gaps
Ideal for:
- anyone with a lab science background working in GMP manufacturing
…who want: fill in the regulatory, risk management, and validation gaps in your knowledge as fast as possible.
Duration: 10 weeks
Hours per week: 12
Awarding body: GetReskilled
Learn the air, water and steam systems that underpin aseptic/sterile processing
Ideal for:
- anyone with a sound understanding of GMP rules and regulations
…who want: an in-depth program on how the systems that underpin aseptic/sterile processing are designed and run.
Duration: 13 weeks
Hours per week: 16
Awarding body: GetReskilled
Generate process validation protocols and prepare a summary validation report
Ideal for:
- anyone with a sound understanding of GMP rules and regulations
…who want: generate process validation protocols and prepare a summary validation report.
Duration: 10 weeks
Hours per week: 14
Awarding body: GetReskilled
Pharma Manufacturing Essentials Course
Ideal for:
- You’re an engineering or laboratory science graduate applying for jobs and who wants a career in the high-paying pharmaceutical and medical device manufacturing industry
OR - You are a university graduate with a non-laboratory science or engineering qualification.
OR - You are a school leaver trapped in a low-level job with little chance of a pay rise or a promotion.
…who want: a career in the high-paying pharmaceutical and medical device manufacturing industry
Duration: 10 weeks
Hours per week: 10
Awarding body: GetReskilled
Take Your Pharmaceutical Manufacturing Career to Management Level
Ideal for:
- anyone looking for a new career in pharma
…who want: to expand their career opportunities in the pharmaceutical or medical device manufacturing industry.
Duration: 104 weeks
Hours per week: 14
Awarding body: Technological University Dublin, Ireland
5-Week Advanced Career Coaching Program For the Pharma Industry
Ideal for:
- Candidate’s who have been sending out applications but getting no response
…who want: to start a new career in the pharma industry but don’t know where to start.
Duration: 5 weeks
Hours per week: 15
Awarding body: GetReskilled
Advanced Writing Skills for the Pharmaceutical Industry
Are you looking for career progression in the Pharma manufacturing industry? Study online for your next step up the career ladder with good writing skills.
Duration: 5 weeks
Hours per week: 15
Awarding body: GetReskilled
START HERE ↓
Choose your background to find the best-fit course, then click the red button
Or keep scrolling and choose from our programs and courses.