What is Process Validation in Pharmaceutical Manufacturing?
By: Gerry Creaner B.Chem Eng and Donagh Fitzgerald B.Prod Eng. Last Updated: July 2024
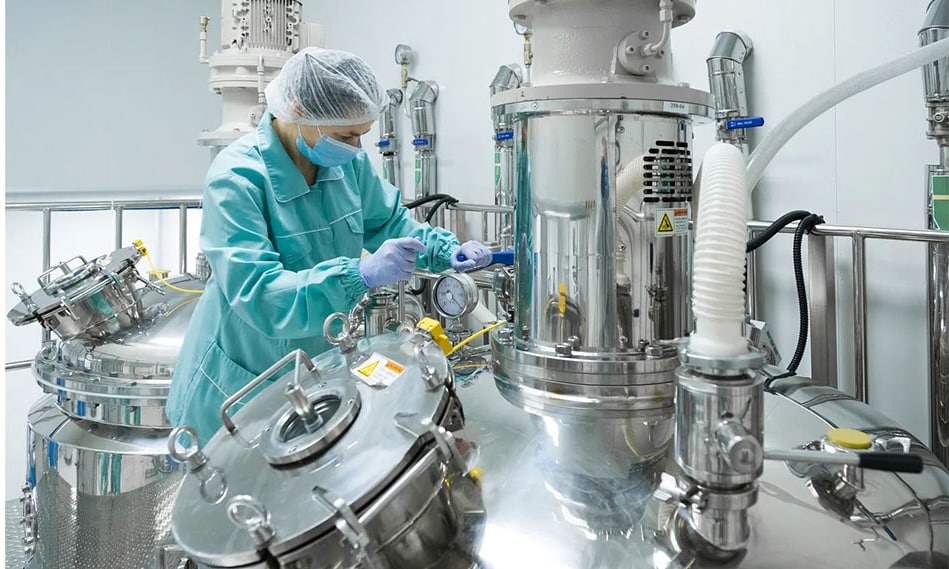
Process Validation is a systematic approach that makes sure a manufacturing process consistently produces high-quality pharmaceutical products that meet safety and efficacy standards regardless of variations in inputs from the manufacturing system.
The goal is to establish documented evidence that the manufacturing process reliably produces safe and effective products. It includes three stages:
- Process Design: Defining the commercial manufacturing process using knowledge from development and scale-up activities.
- Process Qualification: Evaluating the process design to ensure it can consistently produce quality products in commercial manufacturing.
- Continued Process Verification: Ongoing monitoring during routine production to ensure the process remains in control.
Process validation follows a strict set of checks that need to be followed (called a protocol). This protocol includes instructions on how to manufacture the medicine and the type of equipment that is to be used in making it.
The protocol will have been developed by scientists who originally researched and made the medicine and will have been approved as part of a submission to the FDA. It now serves as the “how to” for making this medicine to make sure it consistently meets all of the quality requirements, every time.
Before commercial distribution, manufacturers must have a high degree of confidence in their manufacturing process, demonstrated by data from laboratory, pilot, and commercial-scale studies.
Manufacturers must maintain the process in control throughout its lifecycle, adapting to changes in materials, equipment, environment, personnel, and procedures. Ongoing programs should collect and analyze data to monitor and improve the process, even for legacy products, leveraging existing knowledge and experience.
Let’s take an in-depth look.
And as with that “What is Pharmaceutical Validation?” article, keep a lookout for our simplified baking analogies in blue boxes like this, throughout this article.
(As well as their accompanying Great British Bake Off gifs!).
Think of a validation protocol like a really detailed recipe.
While a standard recipe would lay out ingredients and method, our detailed recipe is also going to set out expectations for the equipment we use and what our cake mix should be like at various points throughout the baking process.
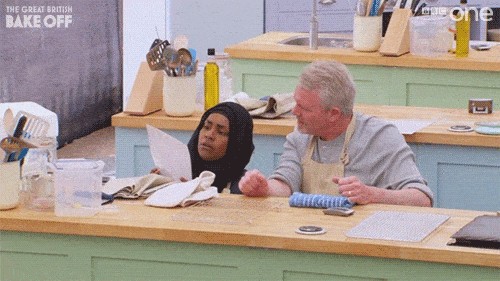
Image: Giphy
3 Stages of Process Validation in Pharmaceutical Manufacturing
Process Validation can be sub-categorised into 3 stages:
- Stage 1 – Process Design
- Stage 2 – Qualification
- Stage 3 – Continued Process Verification
Before we take a closer look at each part, it’s worth acknowledging that some of these stages have multiple parts and it can get a little confusing.
So let’s lay out the full outline upfront, and we’ll revisit this each time we move on to a different section…
- Stage 1 – Process Design
- Stage 2 – Qualification
- Part 1 – Facility Design
- Part 2 – Qualification of Utilities & Equipment
- Subsection 1 – Installation Qualification
- Subsection 2 – Operational Qualification
- Subsection 3 – Performance Qualification
- Part 3 – Process Performance Qualification (PPQ)
- Stage 3 – Continued Process Verification
Stage 1 – Process Design
- Stage 1 – Process Design (← we are here)
- Stage 2 – Qualification
- Part 1 – Facility Design
- Part 2 – Qualification of Utilities & Equipment
- Subsection 1 – Installation Qualification
- Subsection 2 – Operational Qualification
- Subsection 3 – Performance Qualification
- Part 3 – Process Performance Qualification (PPQ)
- Stage 3 – Continued Process Verification
“Stage 1 – Process Design: The commercial manufacturing process is defined during this stage based on knowledge gained through development and scale-up activities.” – FDA
Process design is the initial stage of any process validation protocol.
The ultimate aim of the process design stage is to develop and document a manufacturing process that can be used in commercial manufacturing to consistently produce a quality medicine every time.
The “commercial manufacturing” bit is important.
The process needs to be able to produce enough medicine for lots of patients, not just a few.
Many of the key factors being considered throughout the process design phase (known as critical product attributes) are determined during the earlier product development activities.
In these earlier stages, only small quantities of the medicine are made and tested on patients during clinical trials. The aim of these trials is to prove that the medicine is safe to use and effective in treating patients.
The challenge at this stage (since a pharmaceutical product has already gone through lots of development and testing) is to maintain the quality of the medicine that was established during small lot manufacturing, now that large batches are to be made.
To think about how complex this can be – consider the challenge of baking lots of cakes (all of which have to be just as good as each other), compared to baking just one cake.
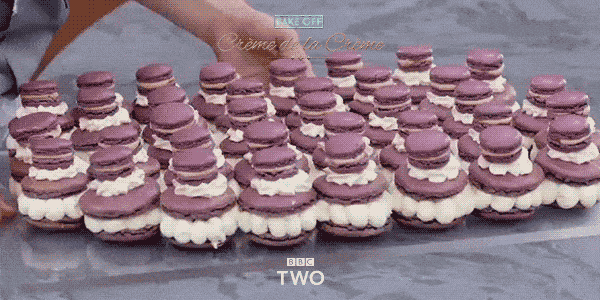
Image: Giphy
“Product development activities provide key inputs to the process design stage, such as the intended dosage form, the quality attributes, and a general manufacturing pathway.” – FDA
Within the process design stage, small scale production processes are designed and tested for their suitability to consistently manufacture a medicine that meets all of the necessary quality requirements.
This stage is often carried out in a laboratory. Making drugs can be very complex and it can require lots of different experiments to get them to work.
Although these experiments are not typically carried out under cGMP conditions (like commercial manufacturing is), they will closely follow good science and will be carefully documented.
When carrying out their experiments in the laboratories, the scientists will already be thinking about the types of equipment that can be used when the process is to be scaled-up for commercial manufacturing of large quantities of the medicine.
So in our baking example, we know the basic recipe.
We’ve used it to make a small number of cakes and had people taste them. People like our cakes, and we’ve not given anyone food poisoning!
Now we want to be able to make lots of the same cake at once.
We have to come up with a process that lets us make lots of cakes in a batch, not just one each time.
We’ll start in a test kitchen and work with our basic recipe to create a baking process that makes a batch of cakes. But we can’t just use anything.
We’ve got to keep in mind what sort of equipment our final kitchen is going to have.
There’s no point in creating a process that depends on a piece of equipment that our final kitchen won’t have.
Mary Berry’s got the idea…
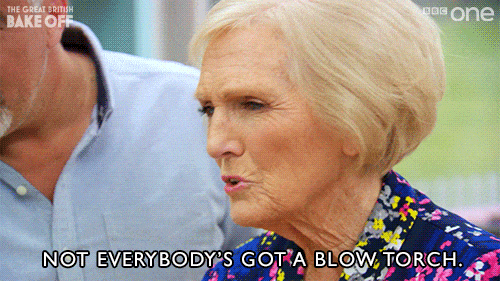
Image: Giphy
This approach will give the best chance of successfully controlling the manufacturing process (and reducing any variability as compared to manufacturing in the smaller lots).
In turn, this control helps to make sure that the critical quality attributes of the medicines continue to be consistently achieved.
“FDA expects controls to include both examination of material quality and equipment monitoring.” – FDA
Completion of this stage will involve testing the quality and consistency of the medicines that are made, as well as the equipment they are made with.
Examples of conditions that might be recorded at this stage include:
- the temperatures at which the medicine is made
- the pressure in the vessel where the medicine is made
- the length of time it takes to make it
The steps documented at this stage will be incorporated within “planned master production and control records”.
These documents will be available for FDA auditors to review.
In addition, any factors influencing how the decisions about the process were made should also be documented.
Examples might include documenting the risk management tool that informed a scientific-based decision to do something a certain way, and how the safety of the patient who would eventually take the medicine was taken into account.
“It is essential that activities and studies resulting in process understanding be documented.” – FDA
This means that later on, if changes to a process are being considered, the data and decisions that led to the initial plan, can be understood.
Perhaps we decide to bake our cakes at 180°C rather than 200°C.
We’ve decided that because we don’t want our cakes to burn on the outside but still be uncooked in the middle. It’s better for the people eating our cakes if they’re cooked at 180°C.
Once we’ve decided that, we’ll make a note of the temperature in our detailed recipe.
But we’ll also make a note about why we chose that temperature.
That means that if someone comes along later and thinks it might be a good idea to change the process and cook our cakes at 200°C instead, they can see why we chose not to.
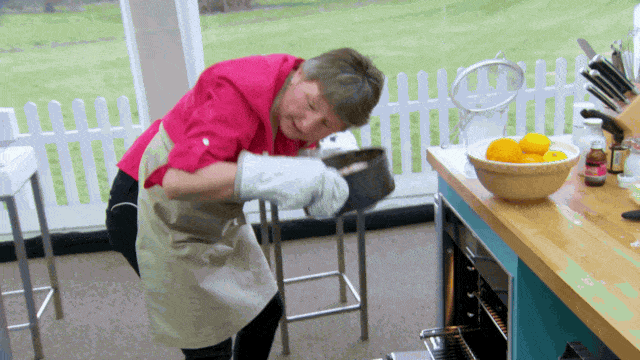
Image: Giphy
Once a process has been successfully completed and each step/condition carefully documented, the process design is ready to be sent on to the next stage.
It is important to note that all conditions throughout the process must be recorded to be able to move onto the next stage. Those who were not originally there have to subsequently be able to review what was done and understand why.
Stage 2 – Qualification
- Stage 1 – Process Design
- Stage 2 – Qualification (← we are here)
- Part 1 – Facility Design
- Part 2 – Qualification of Utilities & Equipment
- Subsection 1 – Installation Qualification
- Subsection 2 – Operational Qualification
- Subsection 3 – Performance Qualification
- Part 3 – Process Performance Qualification (PPQ)
- Stage 3 – Continued Process Verification
“Stage 2 – Process Qualification: During this stage, the process design is evaluated to determine if the process is capable of reproducible commercial manufacturing.” – FDA
Essentially, qualification takes the process that was just designed and tested in stage 1, and reproduces it at commercial manufacturing scale (the size of manufacturing operation that will subsequently be used).
Qualification begins with the designed process and ends with a facility, system or piece of equipment that is ready to begin commercial manufacturing.
As with all parts of manufacturing – qualification involves testing, observing AND documenting.
The Qualification stage is comprised of 3 main parts:
- Facility Design
- Qualification of Utilities & Equipment
- Process Performance Qualification (PPQ)
Stage 2 – Part 1: Facility Design
- Stage 1 – Process Design
- Stage 2 – Qualification
- Part 1 – Facility Design (← we are here)
- Part 2 – Qualification of Utilities & Equipment
- Subsection 1 – Installation Qualification
- Subsection 2 – Operational Qualification
- Subsection 3 – Performance Qualification
- Part 3 – Process Performance Qualification (PPQ)
- Stage 3 – Continued Process Verification
Facility design is where the small scale process designed in the previous (process design) stage is studied and, from it, a large scale commercial manufacturing facility is developed that maintains all the critical quality attributes of the medicine.
Facility design might include selecting things such as:
- equipment to manufacture the medicines
- processes to heat-up and cool-down reaction mixtures
- utilities to ensure clean water (which can to make the medicines as well as clean the equipment between batches)
- systems to filter the air in the manufacturing area (to make sure that it’s clean and will not contaminate the medicines being made)
- the technical specifications and operating requirements of the equipment to be used
Facility design will also decide how big the manufacturing facility needs to be in order to make as much of the medicine as is required.
So we know the process we’re aiming to carry out from the previous steps. Now we have to set up our kitchen to be able to do that. We might consider things such as:
- How will we measure our ingredients
- What mixing equipment will we need
- What oven we’ll use, and where we can leave the cakes to cool
- Making sure our sink is connected to the water supply so we can wash our dishes
Stage 2 – Part 2: Qualification of Utilities & Equipment
- Stage 1 – Process Design
- Stage 2 – Qualification
- Part 1 – Facility Design
- Part 2 – Qualification of Utilities & Equipment (← we are here)
- Subsection 1 – Installation Qualification
- Subsection 2 – Operational Qualification
- Subsection 3 – Performance Qualification
- Part 3 – Process Performance Qualification (PPQ)
- Stage 3 – Continued Process Verification
Qualification of utilities & equipment is when the equipment to manufacture the medicine is installed in the manufacturing facility and is checked to see that it is working properly and can operate as intended.
“Qualification of utilities and equipment generally includes the following activities:
- Selecting utilities and equipment construction materials, operating principles, and performance characteristics based on whether they are appropriate for their specific uses.
- Verifying that utility systems and equipment are built and installed in compliance with the design specifications (e.g., built as designed with proper materials, capacity, and functions, and properly connected and calibrated).
- Verifying that utility systems and equipment operate in accordance with the process requirements in all anticipated operating ranges. This should include challenging the equipment or system functions while under load comparable to that expected during routine production. It should also include the performance of interventions, stoppage, and start-up as is expected during routine production. Operating ranges should be shown capable of being held as long as would be necessary during routine production.” – FDA
This stage can be thought of as checking each of the individual component parts that comes together to make up the manufacturing facility (e.g. the vessels, the piping, the instruments, the electrical wiring etc).
The qualification of utilities & equipment can be further broken down into 3 sub-categories:
Installation Qualification (IQ)
This stage ensures that all equipment has been installed correctly as intended, in accordance with standards set by the manufacturer, and with all necessary documentation.
Say we’ll need an oven to bake our cakes in…
- Have we installed the oven as per the instructions in the user manual?
- And have we installed it where we decided we were going to, in the previous step?
- Is it on a level surface?
- Is it connected to the power and turning on as it should?
- Is the door opening and closing without any difficulties?
- Are all the different functions of the oven working (the fan oven, the grill, etc)?
Remember that we’ll do the same sort of testing for every piece of equipment involved in baking our cakes.
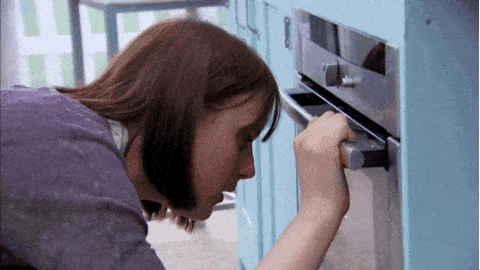
Image: Giphy
Operational Qualification (OQ)
This stage ensures that all parts of the equipment operate/function as they are meant to. This is often done by running water through the equipment.
In our oven example, we’ll test the different functions of the oven, without putting any food in. We’ll:
- Close the door
- Turn on the oven
- Check that the oven heats up as it should and that the door remains closed, keeping the heat inside
- Check that the oven remains at the right temperature for the duration of the test
- See that it cools down as it should after being switched off
- Make sure that it’s not caused any heat damage to the equipment and surfaces around it
Again, similar testing will be done for all the different pieces of equipment used to prepare our cake.
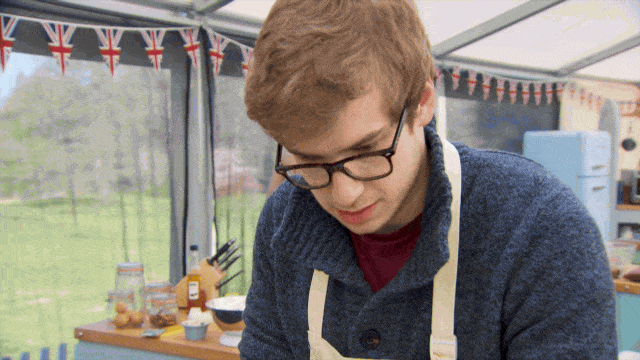
Image: Giphy
Performance Qualification (PQ)
This stage ensures that the equipment functions as intended when the ingredients to make the medicine are used (not just water).
Now we’ll put a cake tin with raw cake mix into the oven and check that the oven still performs as expected and that our cake cooks as expected.
And every step of the process will be considered like this, using actual cake ingredients.
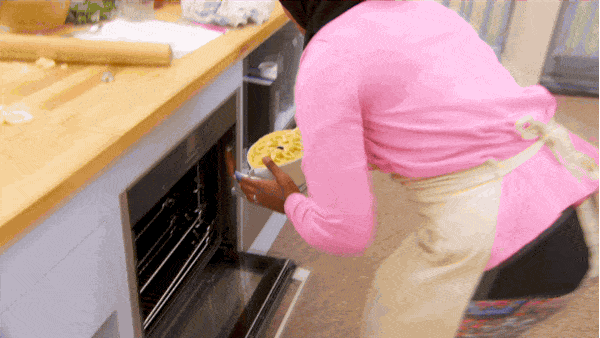
Image: Giphy
Check out this dedicated post for a much more detailed look at the qualification stages IQ OQ PQ – including a more thorough discussion of each, as well as definitions.
When each of these 3 sub-categories of Qualification of Utilities & Equipment have been completed, the team can move on to PPQ, the 3rd part of Stage 2…
Stage 2 – Part 3: Process Performance Qualification (PPQ)
- Stage 1 – Process Design
- Stage 2 – Qualification
- Part 1 – Facility Design
- Part 2 – Qualification of Utilities & Equipment
- Subsection 1 – Installation Qualification
- Subsection 2 – Operational Qualification
- Subsection 3 – Performance Qualification
- Part 3 – Process Performance Qualification (PPQ) (← we are here)
- Stage 3 – Continued Process Verification
“Process qualification: Confirming that the manufacturing process as designed is capable of reproducible commercial manufacturing.” – FDA
Having previously validated each component of the process individually, this stage tests that the system as a whole can consistently make medicines that meet the critical quality attributes. Usually 3 consecutive batches of medicines are required to confirm the success of the process design and qualification stages.
“The PPQ combines the actual facility, utilities, equipment (each now qualified), and the trained personnel with the commercial manufacturing process, control procedures, and components to produce commercial batches. A successful PPQ will confirm the process design and demonstrate that the commercial manufacturing process performs as expected.” – FDA
Essentially PPQ brings together the manufacturing process (including qualified facility, equipment, and utilities), process controls and personnel. It is the method of testing all aspects of the facility as one integrated system.
The aim of this stage is to manufacture a small number of commercial batches of medicine, known as PPQ batches.
Now it’s time to make batches of cakes.
We’ll get the people who are going to bake our cakes every day to use the process we’ve developed and the equipment we’ve installed.
They’ll make 3 batches in total, from start to finish, and we’ll carry out lots of tests and checks to make sure that our cakes are turning out like they’re meant to.
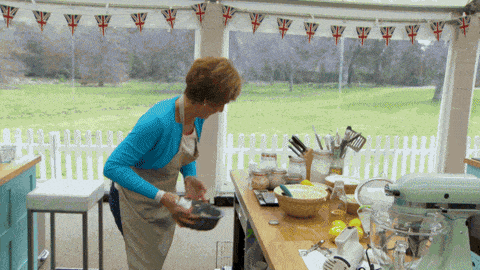
Image: Giphy
The FDA outlines that following a written protocol, approved by all appropriate departments, is essential to guide the manufacturing of PPQ batches.
“We recommend that the protocol discuss the following elements:
- The manufacturing conditions, including operating parameters, processing limits, and component (raw material) inputs.
- The data to be collected and when and how it will be evaluated.
- Tests to be performed (in-process, release, characterization) and acceptance criteria for each significant processing step.
- The sampling plan, including sampling points, number of samples, and the frequency of sampling for each unit operation and attribute…
- Criteria and process performance indicators that allow for a science- and risk-based decision about the ability of the process to consistently produce quality products…
- Design of facilities and the qualification of utilities and equipment, personnel training and qualification, and verification of material sources (components and container/closures), if not previously accomplished.
- Status of the validation of analytical methods used in measuring the process, in process materials, and the product.
- Review and approval of the protocol by appropriate departments and the quality unit.” – FDA
Manufacturing of the PPQ batches of medicines replicates the commercial manufacturing process entirely. Features of this include:
- production of commercial manufacturing scale batches of medicines
- following cGMP procedures
- conducted by staff who would routinely perform these manufacturing tasks
- normal operating utility (air and water) systems
The PPQ stage will generally require more testing and greater analysis of the performance of the process than a standard commercial batch though. This increased testing is required to give statistical significance to the analysis that follows.
Success during the testing of the PPQ batches will confirm (with statistical significance) that products from within a batch are consistent and meet the predefined product quality specifications. It will also confirm consistency between batches.
Our regular bakers will be baking the cakes.
We’ll have them wear the aprons and the hair nets that they’ll have to when we start selling our cakes.
And they’ll bake the same size of batch as we plan to make regularly.
We’ll also carry out more tests here than we will once we’re routinely making our cakes, because we’re still trying to make sure our process and equipment and producing exactly what they’re meant to.
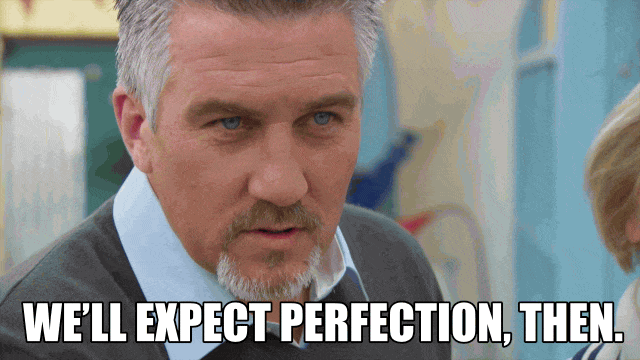
Image: Giphy
The number of PPQ batches required depends on the type of validation. But for prospective validation (the most common type), 3 consecutive batches are typically required.
As with every stage of validation, documentation is extremely important. A report on the completed PPQ activities is necessary.
“This report should:
- Discuss and cross-reference all aspects of the protocol.
- Summarize data collected and analyze the data, as specified by the protocol.
- Evaluate any unexpected observations and additional data not specified in the protocol.
- Summarize and discuss all manufacturing nonconformances such as deviations, aberrant test results, or other information that has bearing on the validity of the process.
- Describe in sufficient detail any corrective actions or changes that should be made to existing procedures and controls.
- State a clear conclusion as to whether the data indicates the process met the conditions established in the protocol and whether the process is considered to be in a state of control. If not, the report should state what should be accomplished before such a conclusion can be reached. This conclusion should be based on a documented justification for the approval of the process, and release of lots produced by it to the market in consideration of the entire compilation of knowledge and information gained from the design stage through the process qualification stage.
- Include all appropriate department and quality unit review and approvals.” – FDA
The medicines manufactured in the facility must pass this stage before they can be distributed commercially. If a PPQ stage is unsuccessful, the team will return to design and qualification stages to make adjustments.
Once PPQ has been passed, the medicines from the new manufacturing facility are available for sale to patients (i.e. commercial distribution). All successful batches of medicines made during the PPQ stage are also allowed to be distributed commercially.
If all of our cake testing (including testing the equipment and the cake mix at various points throughout the process) produces results within the range our detailed recipe say they should, we’ll pass our PPQ.
If we successfully pass our PPQ, we can go on to bake as many batches of cakes as we want to. And we’d be allowed to sell them because we’re sure they’re turning out like they should.
AND we’d be allowed to sell the 3 batches of cakes we made as part of the PPQ process.
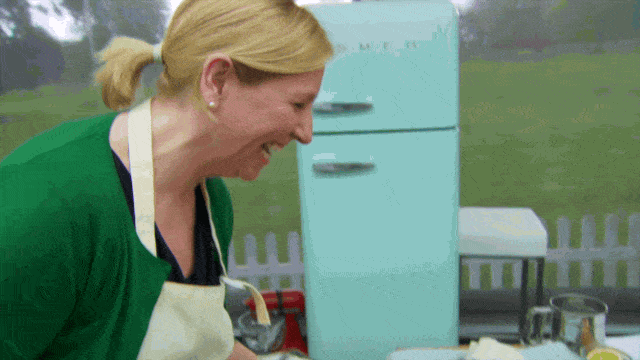
Image: Giphy
Stage 3 – Continued Process Verification
- Stage 1 – Process Design
- Stage 2 – Qualification
- Part 1 – Facility Design
- Part 2 – Qualification of Utilities & Equipment
- Subsection 1 – Installation Qualification
- Subsection 2 – Operational Qualification
- Subsection 3 – Performance Qualification
- Part 3 – Process Performance Qualification (PPQ)
- Stage 3 – Continued Process Verification (← we are here)
“Stage 3 – Continued Process Verification: Ongoing assurance is gained during routine production that the process remains in a state of control.” – FDA
The final stage of validation is Continued Process Verification.
This stage is ongoing throughout the manufacturing lifecycle of the facility. The aim of this stage is to ensure that the previously validated system remains in a reliable and validated state. And, ultimately, that the facility continues to produce reliable and consistent medicines.
Failure to complete this stage of validation could result in compromised batches of unreliable quality medicine, that are unsuitable for the market.
CPV picks up from where PPQ (and its enhanced testing) finishes…
“The increased level of scrutiny, testing, and sampling should continue through the process verification stage as appropriate, to establish levels and frequency of routine sampling and monitoring for the particular product and process. Considerations for the duration of the heightened sampling and monitoring period could include, but are not limited to, volume of production, process complexity, level of process understanding, and experience with similar products and processes.“ – FDA
As the duration of manufacturing extends, companies will decide on an ongoing CPV schedule.
The activities of this stage focus on two key goals:
1. To maintain equipment and facilities in their validated state
2. To quickly highlight variation in product or process data, allowing corrective action to be taken
As with previous areas of validation, CPV activities are focused primarily in areas of the manufacturing process where the critical quality attributes of the medicines are most at risk of variation. But manufacturers have to remain mindful that unforeseen variations can occur over time, from unexpected parts of the process.
“A system or systems for detecting unplanned departures from the process as designed is essential to accomplish this goal.” – FDA
Activities involved in Continued Process Verification might include things such as:
- Regular equipment maintenance
- Routine testing of in-process materials and final product sampling (comparing both within and between batches)
- Routine gathering and analysis of in-process data
- Equipment swabbing
- Cleaning
Successful CPV provides documentation that critical quality attributes remain controlled throughout the manufacturing process and over its entire lifecycle.
As we continue baking our cakes, we’re going to keep testing (but at a lower level than the testing of our PPQ batches).
We’ll also make sure that we’re maintaining our baking equipment – we’ll keep our oven clean, we’ll routinely calibrate our weighing scales, and we’ll replace parts in our mixer as they’re needed.
We’ll keep a specific eye on the places where we know our cake making is at risk of variation.
But we’ll also watch to make sure that there isn’t variation coming from somewhere that we didn’t expect.
For example… maybe our cake icing stops setting like it’s supposed to, despite following all the relevant cake-icing parts of the recipe.
That’s a variation we weren’t expecting.
We need to go back and look at the process, figure out where that variation is coming from, and update our detailed recipe to stop that variation from happening again.
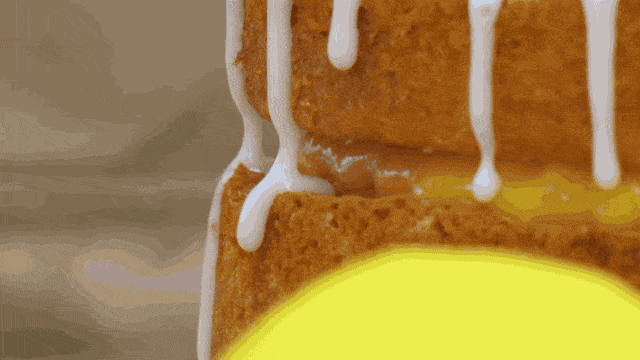
Image: Giphy
It is only through ongoing assured control of critical quality attributes, that a pharmaceutical manufacturer can be certain that their medicines remain fit for purpose, effective in use and safe for patients.
This stage of validation is never complete.
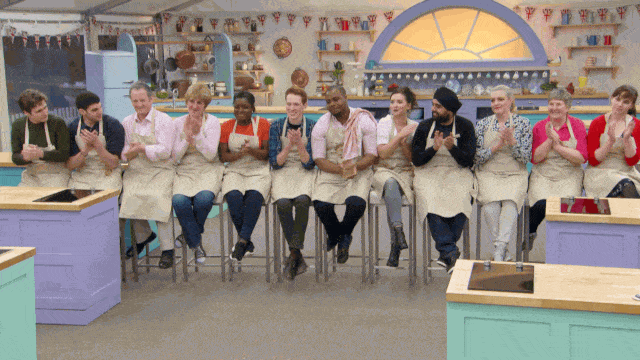
Image: Giphy
Further Reading
You might also be interested in reading:
- What is pharmaceutical validation?
- What are IQ OQ PQ?
- What is an equipment validation protocol?
- Validation regulations
- The 8 most “in demand” skills for validation professionals
- What is computer system validation or CSV?
- What is a Validation Master Plan?
About the Author
Gerry Creaner
President
Senior Lecturer with GetReskilled
Gerry Creaner has over 40-years of experience in the Life Sciences Manufacturing industry across a range of technical, managerial and business roles. He established a very successful engineering consultancy prior to founding GetReskilled, an online education and learning business, with offices in Singapore, Ireland and Boston (USA), focussed on the manufacture of safe and effective medicines for the public.
He is also a founding Director of two Singapore based philanthropic organizations, the Farmleigh Fellowship and the Singapore-Ireland Fund, both of which deepen the well established and historical Singapore – Ireland relationship and deliver long-term benefits to both countries.
Gerry has an undergraduate degree in Chemical Engineering (UCD, 1980) and an MSc (Management) from Trinity College Dublin (2003) and is currently doing research for his Ph.D.
Donagh Fitzgerald
Head of Marketing & Product Development
Mechanical/Production Engineer
Donagh looks after the marketing and product development including the training and pedagogical elements of our programs and makes sure that all GetReskilled’s users can have a great online learning experience. Donagh has lived and worked in many countries including Ireland, America, the UK, Singapore, Hong Kong and Japan. Donagh has also served as the Program Manager for the Farmleigh Fellowship based out of Singapore.
Donagh holds Degrees in Production Engineering and Mechanical Engineering from South East Technological University, Ireland.