What is Pharmaceutical Validation?
By: Gerry Creaner B.Chem Eng and Claire Wilson BSc. Last Updated: October 2024
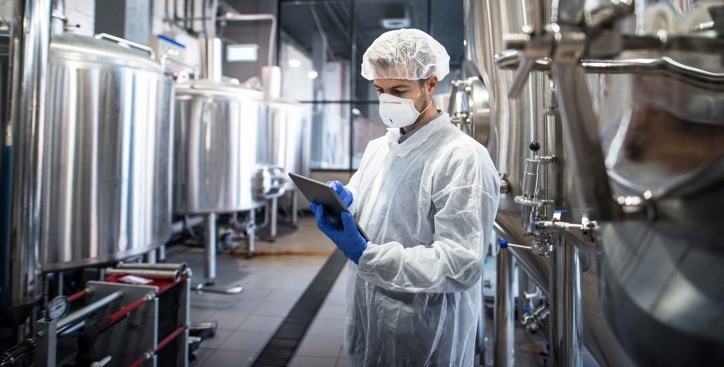
Image: Dickson
Defining Pharmaceutical Validation
Whether we’re talking about a piece of equipment designed to do something, a process/recipe to make something, or a computer programme to control something – the pharmaceutical industry uses validation.
It can be a complicated area to understand if you don’t have direct experience with it. So as we explore the area of validation, we’re going to think about the concepts as if we were baking a batch of cakes.
Keep an eye out for the text in blue boxes (like the one below) for our simplified cake examples and some old-school Great British Bake Off gifs!
Pharmaceutical Validation Training Courses
If interested, the Application DEADLINE for our next Equipment Validation Training Course – for starter validation, CQV and C&Q roles and our NFQ L7, 15 ECTS Pharmaceutical Validation Training Course – for more senior validation, CQV and C&Q roles is Wednesday 9th July
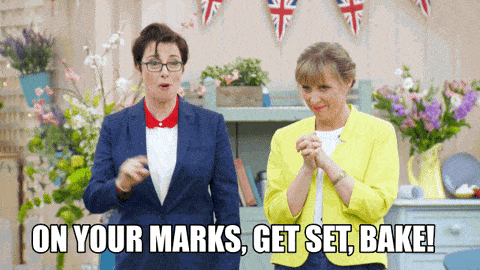
Image: Giphy
At its most simple – validation is testing whether something works, as well as writing down what you did and what happened when you did it.
This means you can prove that it worked to others who weren’t there.
For a more technical answer, let’s look at how the US Food & Drug Administration (the FDA – the US regulatory body for pharmaceutical manufacturing) defines Process Validation (the most common type of validation, used on processes)…
“Process validation is defined as the collection and evaluation of data, from the process design stage through commercial production, which establishes scientific evidence that a process is capable of consistently delivering quality product. Process validation involves a series of activities taking place over the lifecycle of the product and process.” – FDA
So we can see that there are really 3 main parts in this definition of validation.
Validation is…
creating an evidence trail…
to show that an action, process, or system…
leads to a consistent and reproducible result.
This ‘result’ is usually taking a measurement or assessing product quality. It is then compared against a predetermined specification (the expected outcome – which is always decided before the test is done).
So we’re baking our batch of cakes…
Validation is like following the world’s most in depth recipe.
We don’t just test the final cake – we test things throughout the baking process, write down the results and compare them against what the recipe says they should be.
Perhaps we’re testing the temperature of the oven, the runniness of our cake mixture, or the speed of the mixer.
If each of these tests (and many more) match with what the recipe tells us to expect, the cakes at the end are much more likely to turn out the way we want.
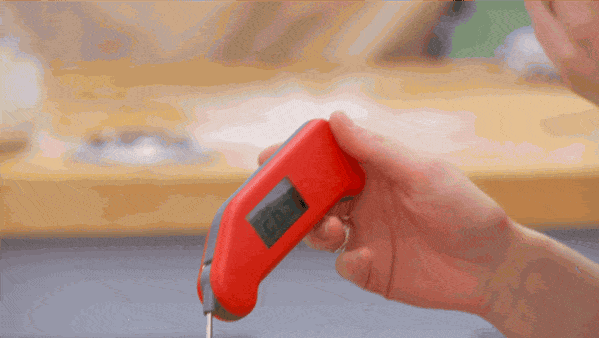
Image: Giphy
And in pharmaceutical manufacturing, a consistent and reproducible result is very important because medicines are not really like cakes. You can’t have a “good batch” for tablets and a “not so good batch”.
Every tablet, every batch, must be good.
Why do we need Validation in Pharmaceutical Manufacturing?
We need validation in pharmaceutical manufacturing because the medicines we make must be the same high quality every time we make them.
Whether they’re made on a Monday morning or a Friday evening…
whether it’s during the day when everyone is watching or in the middle of the night-shift when no one is looking over your shoulder…
whether you’re a new member of staff or someone with 15 years of experience…
the medicine that you make and the equipment that’s used to make it must always be of the same high quality.
This high quality is important so that the medicine is safe for patients to take, will help to make them better, and will not harm them in any way (i.e. they’ll be fit for use and function as expected).
So we have to follow the detailed recipe, whether we have years of experience or its our first time baking.
We want a delicious cake at the end, that tastes exactly like we expect it to.
But more than that, we also need to be sure it’s not going to give us food poisoning.
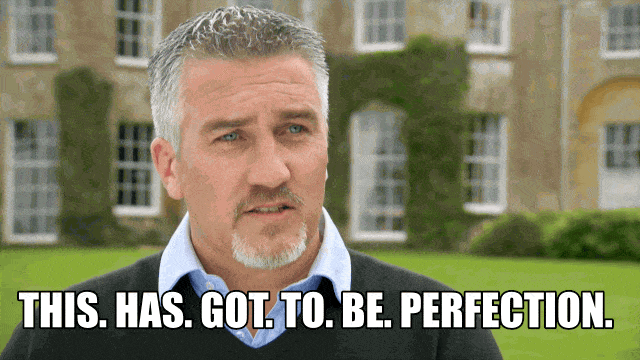
Image: Giphy
We can test final medicines at the end of the production process but final end product testing just isn’t enough.
Every time you test medicines you have less to give to patients. If you are just testing quality through final products, you have to test a lot of them.
However, if you can confirm that a medicine is safe to use every time you made it a certain way AND that you made it the same way every time, it’s a reasonable assumption that the medicine you made this time (in the same way) is also safe for patients to use.
This is what happens when you use a “validated process” to make the medicines.
To be sure that the final medicine is safe and effective for patients to take, we also have to check in on it at multiple points along its way to becoming a final product (i.e. are the ingredients used and the “in-process” materials all the same as expected?).
And finally, we have to rigorously scrutinize the processes, systems, and equipment used throughout manufacturing.
We need to confirm that everything we did was the same as on other occasions when we produced safe medicines using this “validated process”.
At all points, validation tests are comparing a result against a predetermined specification (or an expected result range).
If we were checking the quality of our batch of cakes by slicing open each one, we’d never have a full cake to sell to a customer.
But if we know the recipe gave us great cakes every time we followed it, and we always follow the recipe strictly, we can be confident that the cakes produced will be good.
This would reduce the number of cakes we have to slice open at the end just to check.
So rather than just testing the cakes at the end, we test the quality of the ingredients – the flour, the eggs, the sugar, etc.
And we test different things about the mixture as we follow the recipe…
- Is it as runny as it’s meant to be?
- Is it the colour it’s meant to be?
- Is it as smooth as it’s meant to be?
The detailed recipe will tell us what to expect, and we’ll compare our mixture.
We’ll also test the equipment we’re using and compare it against what the recipe says…
- Are we using the right size tin?
- Is the oven as hot as it’s meant to be?
- Have we left the cake in the oven long enough?
Our “world’s most detailed recipe” is going to give us a range to expect for the results of each of our tests.
For example, the oven temperature must be between 179.5℃ and 180.5℃.
Is our temperature in that range?
We’ll check…
and we’ll document that we checked…
and we’ll also document what temperature our oven was when we checked.
If our cakes match what the recipe expects at every step, we can be more confident that the final cakes are as tasty as we expect. We don’t need to slice open every single one.
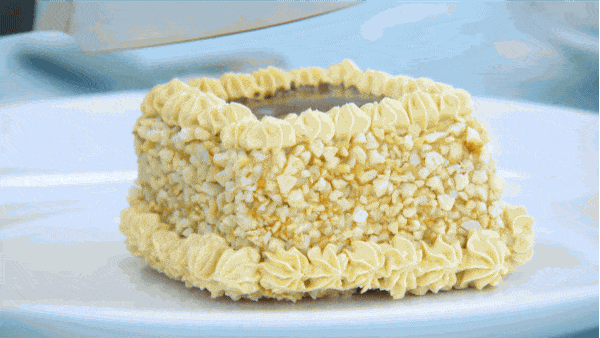
Image: Giphy
Only by looking at – and documenting – the whole manufacturing process in this way, can we say for sure that a final medicine will be safe and effective for patients to take.
“Homogeneity within a batch and consistency between batches are goals of process validation activities.” – FDA
Most medicines are made using a batch process.
This is similar to making a batch of scones/brownies on a baking tray, you get lots of individual end products but they’ve all come from the same mixture in the mixing bowl.
Basically, validation activities are making sure that everything in one batch is the same. BUT they’re also making sure that those things are the same as other batches manufactured by the same process.
To highlight why, you only have to consider our TV baking programme…
Even when contestants are given the same ingredients and the same vague recipe – there can be a huge variation in the cakes that are produced.
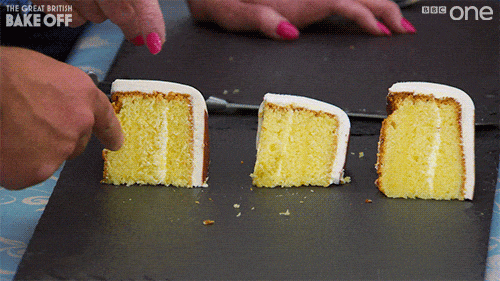
Image: Giphy
While baking shows make for good television, it would be unacceptable if medicines varied that much.
We need much stricter control on the process.
Therefore, consistency between batches is just as important an outcome of validation activities.
To achieve this, each step in the process can be subject to validation.
How Do Companies Actually Achieve This?
When talking about “validation tasks or activities”, we are basically referring to testing, observing, and documenting a measurement and then comparing it against an expected outcome.
We compare what actually happened to what should have happened – to make sure they’re the same.
Validation tasks are carried out during all stages of a product lifecycle – from research and development, through to manufacture and distribution.
As a result, they are tasks that many different departments within a company can have a role in.
“We recommend an integrated team approach to process validation that includes expertise from a variety of disciplines (e.g., process engineering, industrial pharmacy, analytical chemistry, microbiology, statistics, manufacturing, and quality assurance). Project plans, along with the full support of senior management, are essential elements for success.” – FDA
It’s also important to note that validation is not just necessary when building new manufacturing processes.
It is also used to make sure that any changes to systems, equipment, or processes within an established (and previously validated) manufacturing system, do not change the quality or consistency of the medicine that is produced.
We begin writing our detailed cake recipe when we bake our new cake for the first time.
And we update it until we’re sure we’ve got the recipe right.
Then we follow it every time we make a batch of cakes, even when we’re a busy bakery making 100 cakes a day.
And if we decide to get a new mixer, we have to go back and make sure that all the tests in the recipe are still valid, and that none of the expected ranges have changed.
We’ll need to update our recipe to account for the new mixer.
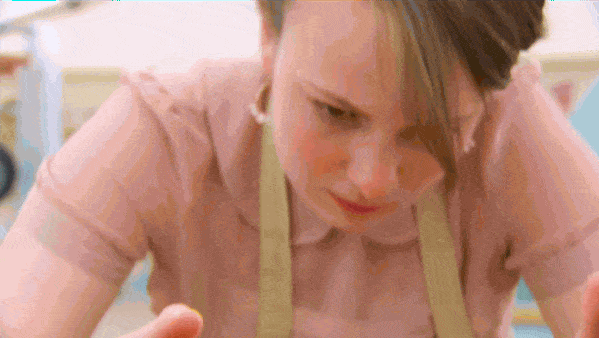
Image: Giphy
What and when do we validate?
If we consider a range where one end is “validate nothing” and the other is “validate everything”, where should we aim for?
Well “validate nothing” isn’t an option. We’ve already established that validation activities are essential for manufacturing safe and effective medicines.
What about “validate everything”?
It seems like a sensible option – we’d know our process worked and we could prove it.
BUT validating things takes time and money. The more we validate within any given process, the more manufacturing will cost. And if manufacturing costs more, the medicine will cost more. If the medicine costs more, fewer patients will have access to it.
So the goal is to validate to a point where we can be sure we’re consistently delivering safe medicines (always the highest priority) but not validating beyond that, where manufacturing costs rise without any additional product safety benefits.
The next question then is how do we decide what is critical to validate, in a way that’s transparent and objective?
The answer is risk management tools.
By applying risk management tools you can decide (in a scientific way) which items are critical, and should therefore be validated. This scientific approach also means that these decisions can be justified to an FDA auditor (or other regulatory bodies) if necessary.
An FDA auditor might have a different opinion about which items are critical – there is often no single right answer to the question of what is critical and what isn’t. BUT the auditor will respect your decision-making process if you can show an analysis using science-based risk management tools.
Using risk management tools, we can define a list of Critical Quality Attributes (CQA) for making safe medicines.
“A CQA is a physical, chemical, biological, or microbiological property or characteristic that should be within an appropriate limit, range, or distribution to ensure the desired product quality.” ICH
Critical quality attributes are the things that are essential for a pharmaceutical product (the medicine) to have its desired effect.
Any variation in these product qualities would alter how well the medicine performs for the patient. So it’s essential that throughout the manufacturing process, these critical quality attributes are monitored and remain the unchanged.
To achieve this, we validate every point where a CQA could be altered.
There are certain things we’ll know about our ideal cake mixture at different points in the baking process. And we’ll know that if any of those things is wrong, the cake would not be a success. So if we noticed one of these things wrong, we’d have to stop and start again – there’s no point in keeping on baking, because the cake will not turn out well.
These things are the CQA’s for baking a successful cake.
As an example…
We know how smooth our mixture should be once all the ingredients are in.
If our mixture isn’t that smooth (if there are lumps), there’s no point in putting it into tins and into the oven. A “lumpy” cake mix will not lead to a nice cake.
Smoothness of the mix is a CQA for baking a good cake.
So once all the ingredients are in, we’d test the smoothness of our mixture to make sure it’s right.
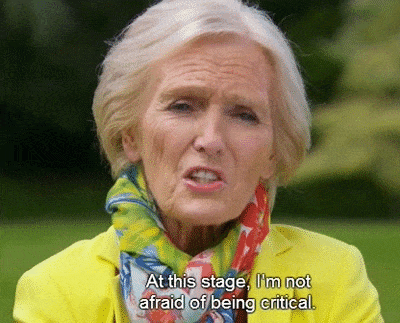
Image: Giphy
When making medicines, identifying the critical quality attributes begins in early product/process development. The FDA understands this and requires that…
“Manufacturers should:
- Understand the sources of variation
- Detect the presence and degree of variation
- Understand the impact of variation on the process and ultimately on product attributes
- Control the variation in a manner commensurate with the risk it represents to the process and product” – FDA
Basically – manufacturers have to establish the things that MUST be controlled for the medicine to be safe to use and to function as expected (remembering that pharmaceutical products will already have gone through extensive clinical trials to prove their safety for patients and to determine how much of the medicine is needed to achieve the desired effect).
Finally, they have to validate the parts of the process that could impact the CQAs, to make sure that all CQAs remain unchanged throughout.
If we think more about the smoothness of our cake mixture, we’ll know the “right” amount of flour to use in our mixture.
So the amount of flour is a CQA and we pay particular attention to things that might change it…
- We carefully measure the amount of flour we need – so we use scales or a measuring cup to add the right amount
- We sieve the flour into the mixing bowl to remove any lumps and we check to make sure we don’t leave any flour in the sieve
- We make sure that we set our mixer to the right speed so it blends all the ingredients together in a controlled way
If the amount of flour in our mixture is critical to the outcome of our cake, then every time there’s a chance that critical quality attribute might change, we put a check in place to make sure that doesn’t happen.
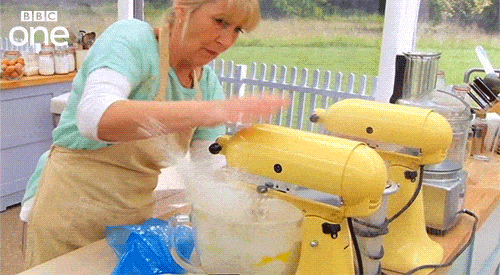
Image: Giphy
Here’s how the ICH talks about this in relation to Active Pharmaceutical Ingredient (API) manufacturing…
“The critical parameters/attributes should normally be identified during the development stage or from historical data, and the necessary ranges for the reproducible operation should be defined. This should include:
- Defining the API in terms of its critical product attributes
- Identifying process parameters that could affect the critical quality attributes of the API
- Determining the range for each critical process parameter expected to be used during routine manufacturing and process control
Validation should extend to those operations determined to be critical to the quality and purity of the API.” – ICH
And that last part is important to note – validation occurs at points where critical quality attributes are ‘at risk’ of alteration/variation.
Of course, there are many other factors that a company might be trying to control throughout the manufacturing process that are not CQAs (e.g. things that relate to the cost of manufacturing the medicine but not the quality of the medicine that is made).
One example might be minimising energy consumption within the manufacturing process.
While this might be important to the company to reduce costs it isn’t essential for maintaining product quality (by maintaining critical quality attributes).
Therefore it does not fall into the category of being a validation activity.
Maybe we only bake cakes on Mondays.
That’s fine – I can tell people coming to bake cakes with us that it’s always on a Monday.
But baking on a Monday isn’t going to change the quality of the cakes.
It’s not critical to the outcome.
So it doesn’t get listed as a rule on our recipe.
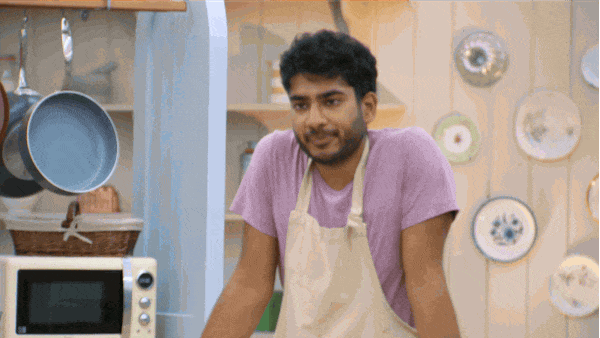
Image: Giphy
As well as identifying the critical quality attributes, companies must establish the acceptable range for each attribute – the high and low values that the critical quality attribute cannot go beyond.
Examples might include the high/low temperature range for the manufacturing process, the specific quantity of ingredients that are used in a batch, and how long they are to be reacted together.
So perhaps our mixer has to run for 90 to 93 seconds at medium speed…
And our oven temperature has to be between 179.5℃ and 180.5℃…
And the cake has to be baked for exactly 30-minutes…
These are all CQAs for baking a good cake and anything that could impact them has to be controlled.
You get the idea!
Image: Giphy
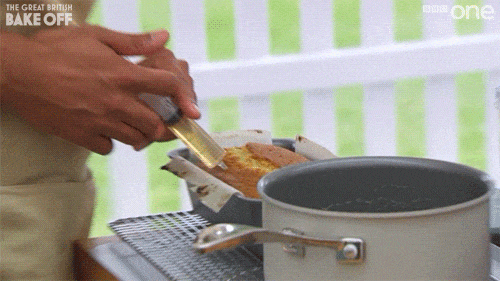
Validation activities will check that the process does not interfere with these critical quality attributes outside the predetermined acceptable levels.
While the initial list of CQAs are produced in early product/process development – further CQAs can be identified and added, as knowledge and experience about how best to consistently make the medicine grows over time.
Further Reading
This is the first is a series of posts about Validation in the pharmaceutical industry.
You might also be interested in:
- What is process validation?
- What is an equipment validation protocol?
- What is a Validation Master Plan?
- The 8 most “in demand” skills for validation roles
- What is computer system validation or CSV?
About the Authors
Gerry Creaner
President
Senior Lecturer with GetReskilled
Gerry Creaner has over 40-years of experience in the Life Sciences Manufacturing industry across a range of technical, managerial and business roles. He established a very successful engineering consultancy prior to founding GetReskilled, an online education and learning business, with offices in Singapore, Ireland and Boston (USA), focussed on the manufacture of safe and effective medicines for the public.
He is also a founding Director of two Singapore based philanthropic organizations, the Farmleigh Fellowship and the Singapore-Ireland Fund, both of which deepen the well established and historical Singapore – Ireland relationship and deliver long-term benefits to both countries.
Gerry has an undergraduate degree in Chemical Engineering (UCD, 1980) and an MSc (Management) from Trinity College Dublin (2003) and is currently doing research for his Ph.D.
Claire Wilson
Content Marketing and Career Coaching
Claire runs GetReskilled’s Advanced Career Coaching Programme – our specially devised job hunting course that helps our trainees take that final step into employment by leading them through the job hunting process. She is extremely enthusiastic about helping people reach their final goal of employment in their new career path.
Claire has a BSc (Hons) in Medical Biology from Edinburgh University and spent 7 years working in the pharmaceutical and medical device industries.