What is a Validation Master Plan (VMP) and How Do You Write One?
By: Donagh Fitzgerald B.Prod Eng. Last Updated: June 2024
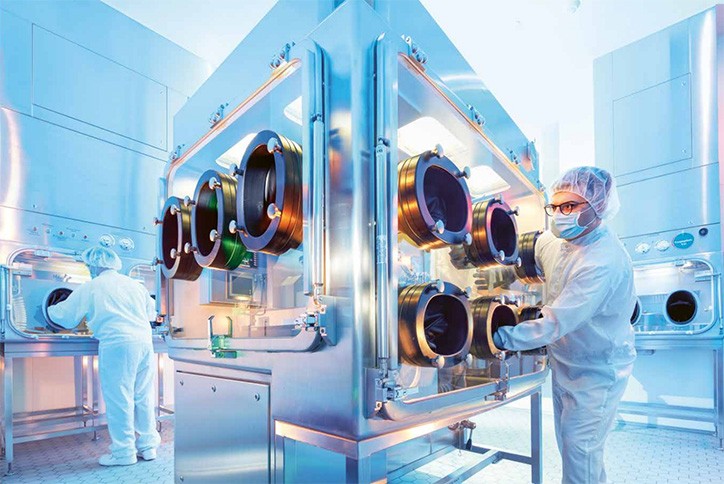
A Validation Master Plan (VMP) is a document that outlines the overall validation strategy for an entire project including the systems and processes to be validated, the schedule to be followed, and the resources needed. It defines the validation requirements and acceptance criteria for the site and makes sure that enough resources are available to complete the entire project.
As a summary document, VMP should be brief, concise and clear and outline a program of work under which there may be several individual validation plans. It explains the validation rationale and defines the preliminary test and acceptance criteria and required validation.
A VMP is commonly used for new product introductions but they are also used to plan and manage ongoing validation projects within companies.
The validation master plan should not repeat information that could be found elsewhere but instead would refer to existing documents such as policy documents, SOPs, validation protocols and reports.
The regulations around the master plan are not very rigid so the best advice is to create a plan that will best fit your organisation and your processes.
Table of Contents
- Why do we need a Validation Master Plan?
- How to write a Validation Master Plan
- Outline the Validation policy
- Define the organisational structure for validation activities
- Identify the facilities, equipment, systems, and processes to be validated
- Define the acceptance criteria
- Describe the document format to be used for protocols and reports
- Develop the validation plan and schedule
- Define change control and deviation management procedures
- Outline qualification and validation strategy, including requalification
- Include references to existing documents
- Conclusion
Why do we need a Validation Master Plan?
-
Regulatory requirement – In the EU Guide for GMPs, Annex 15 (Qualification and Validation) VMPs it is listed as a regulatory requirement. And although the FDA’s 21 CFR part 210, 211 does not formally mention the need for a Validation Master Plan, it is usually the first document an FDA inspector requests when he or she comes on-site at a pharmaceutical facility.
-
Planning – It helps with planning and scheduling a validation project as it identifies anticipated resource needs.
-
Management and staff education – It acts as a top-level document that can pull together the many references, protocols, reports and rationales that make up a validation project.
-
Onboarding – It helps introduce new staff and team members to a project or process when they need to get up to speed quickly and comprehensively.
-
Fosters agreement – It forces the various stakeholders to sit down and agree upon the strategy and the technical rationale required to deliver a successful validation project.
How to Write a Validation Master Plan
The FDA hasn’t defined any regulation regarding the master plan so let’s take our cue from the EU Guide for GMP regulations and look at the master plan under the headings there.
In addition, the Pharmaceutical Inspection Co-operation Scheme (PICs) provides Recommendations on a Validation Master Plan.
The World Health Organisation also provides guidance in its document on Good Manufacturing Practices: Guidance on Validation.
1) Define the Validation Policy
This section gives an overview of the company’s philosophies and intentions and approaches to validation and qualification. It would also outline management’s commitment to incorporating a science and risk-based approach to the validation of operations determined to be critical to the quality and purity of the medicinal product.
The qualification and validation policy should outline the validation approach on facilities, utilities and equipment, production processes, cleaning procedures, analytical methods, control test procedures, computer validation, GxP computerised data, etc.
All personnel responsible for design, review and approval of each validation phase should be documented and approved by management.
It will include definitions of responsibilities such as:
- Responsibilities of the management
- Responsibilities of the validation team
- Responsibilities of other key players who are involved in validation
The VMP should be supported with approval signatures from multidisciplinary functions including:
- Engineering
- Manufacturing
- Quality Control
- Quality Assurance
- Validation
2) Define the organisational structure for validation activities
Each company will have its own organizational structure for the validation teams and the management and control of the validation activities. However, validation is a team effort and it generally requires involvement and close interaction of the validation department with personnel from:
- Quality assurance
- Production
- Packaging
- Product development
- Quality control
- Project Engineering
- Maintenance engineering
So the validation team should include representatives from these departments to provide the necessary expertise and guidance. Usually, each validation project will be assigned a lead member of the validation team who will work together with the rest of the departments and manage the project.
Each protocol and report would be checked by the review team who typically comprises the head of validation, the head of quality assurance, validation team members, and the validation team leader.
In addition, personnel from external validation services may be included. The validation master plan will typically describe the validation activities the company will undertake and these are summarized here.
Organisational Structure of Validation Activities
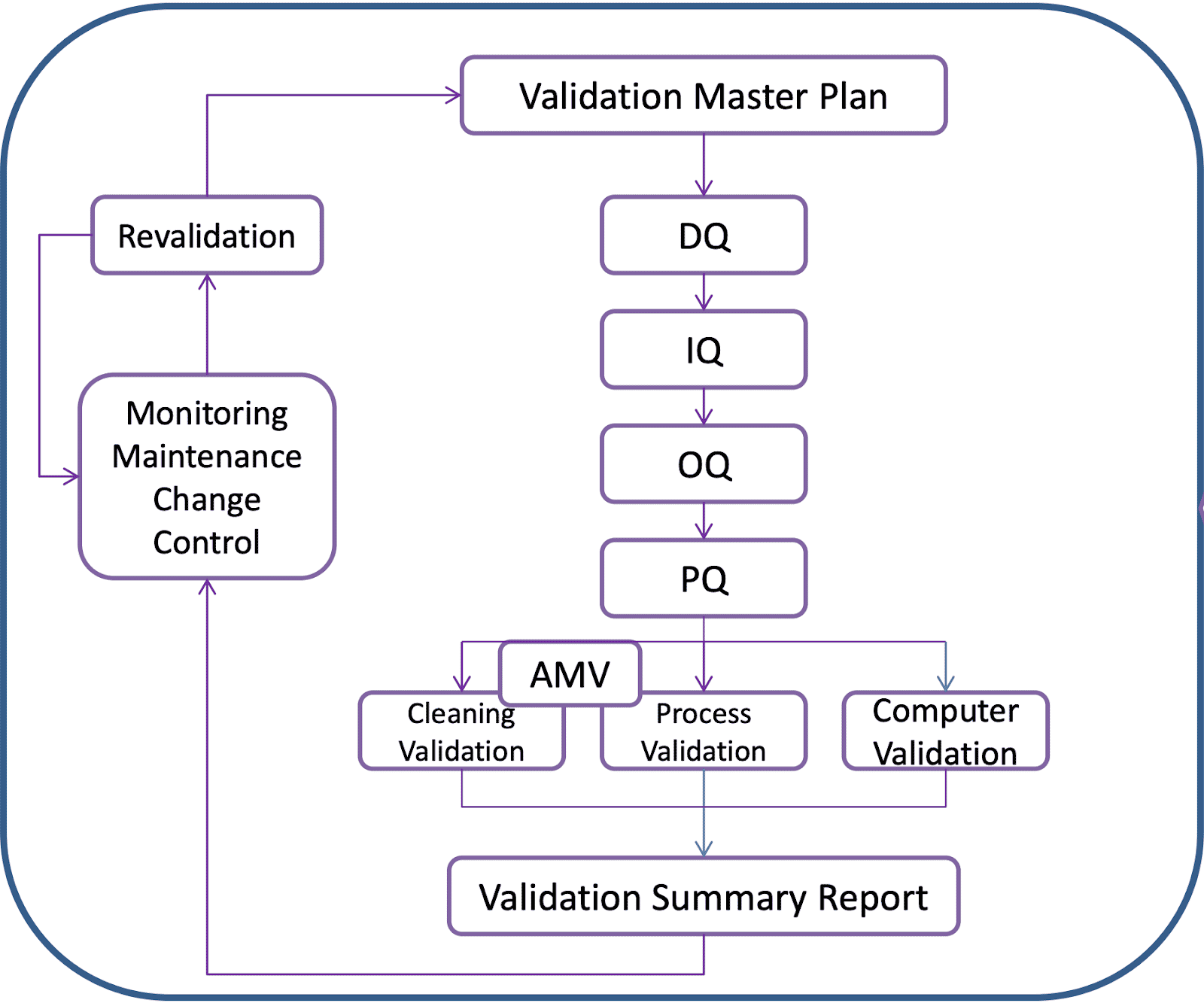
Looking at the graphic above, you would have a Design Qualification (DQ) Installation Qualification, (IQ), Operational Qualification (OQ), and Performance Qualification (PQ).
Then you move into the phase of process validation where you would also at this stage look at Cleaning Validation and Computer System Validation. Cleaning Validation and Process Validation should be underpinned by clear Analytical Method Validation (AMV).
In addition, when the validation is complete you would write a validation summary report. These feed into routine monitoring and maintenance of equipment and change control which would indicate whether revalidation needs to occur and this would then be linked back into an update of the validation master plan or the individual validation plans themselves.
And all these activities should be underpinned by quality risk management and the activities should focus on the aspects that are critical to product quality and patient safety.
3) Identify and summarize the facilities, equipment, systems, and processes to be validated
The next section looks at a summary of the facilities’ systems equipment and processes to be validated.
You would include an overview of the pharmaceutical facility systems utilities and processes. You would include all major areas in this overview for example the central plant, the manufacturing area, the material storage, laboratories etc.
Usually, you would list reference drawings or attach them in appendices as necessary and you would identify critical areas of the facility that will be the GMP versus the non-GMP areas.
Also in the section, you would list all the equipment and processes that need to be qualified and validated and give a summary of the validation and qualification requirements together with operating procedures for the equipment if needed
A matrix approach is useful to identify all components to be validated and the level of validation required and operational procedures associated with these if needed.
Here is an example of a typical matrix that might be included in a validation plan.
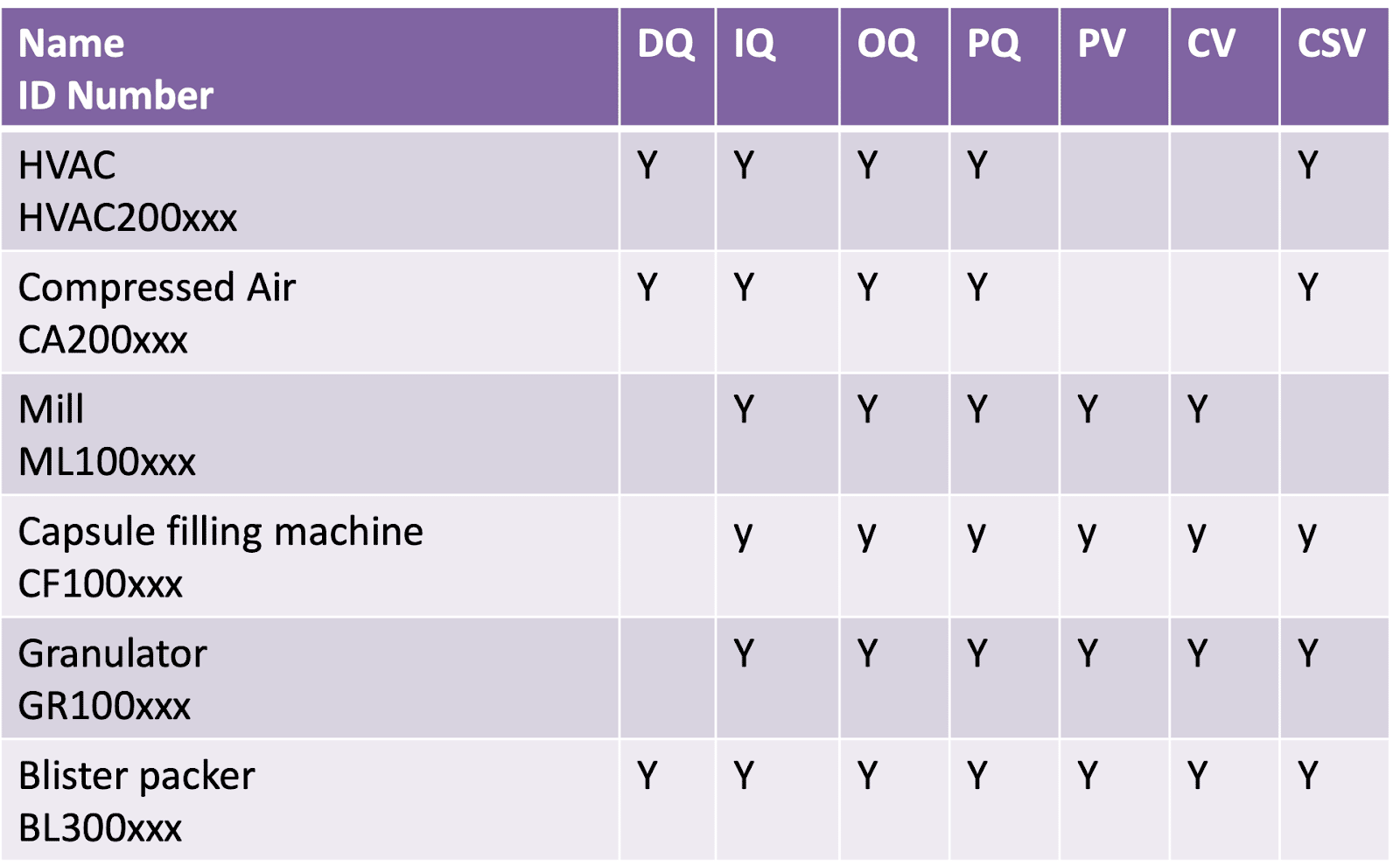
On the left-hand side, we have the piece of equipment or the system listed by number and then we’d indicate whether you need DQ, IQ, OQ, PQ, Process Validation (PV), Computer System Validation (CSV) or Cleaning Validation (CV).
4) Define the Key Acceptance Criteria
Outline the key acceptance criteria for the items listed under the summary of facilities, systems, and processes on-site.
5) Describe the documentation format to be used for protocols and reports
This section of the validation master plan would reference and describe a wide variety of documents used throughout the validation project.
Validation Documents
This section of the validation master plan would usually include reference to SOPs that describes the format of these documents and samples of these documents could also be included. For example:
- DQ IQ OQ and PQ protocols
- Cleaning validation protocols
- Process validation protocols
- Validation protocols
Supporting Documents
The second set of documents that are important is support documents. These could be:
- Development reports
- SOPs on equipment or processes
- Manufacturing instructions – these could come from batch manufacturing records or instructions
- Design specifications – for the facility and equipment
- Material specifications – for the raw materials
- Equipment specifications
- Product specifications – for the release of the products that you’re making
The second set of documents that are important is support documents. These could be:
- Development reports
- SOPs on equipment or processes
- Manufacturing instructions – these could come from batch manufacturing records or instructions
- Design specifications – for the facility and equipment
- Material specifications – for the raw materials
- Equipment specifications
- Product specifications – for the release of the products that you’re making
Document Approval Process
Finally, you would describe the documentation approval process in the Validation Master Plan. In this section, you would describe details of who actually is required to approve each of the validation documents and in particular, you would describe the reasons for their signatures.
For example, if the purpose of the signature is to verify that the information in the protocol is technically correct, signed approval would usually be completed by the production manager or the validation team lead. If the purpose of the signature is to verify that we are complying with regulations, company policies and procedures, signed approval would usually be completed by personal from the regulatory department or the quality department or even by management.
Some of the signatures are there to indicate management support and commitment to the validation process and the documentation. Finally, the quality unit is required to sign and approve all validation documents.
Validation Protocol
Another crucial document is the validation protocol which is a document that specifies how a specific qualification and validation project will be conducted. There are differnets types of protocols..
Equipment Qualification (DQ, IQ, OQ and PQ) Protocols
This protocol will outline the specific acceptance criteria that must be met to demonstrate that the equipment or the system was properly designed, installed and operates correctly.
This is a regulatory requirement outlined in EU GMP regulations annex 15, which stipulates that a written protocol should be established.
The protocol should be reviewed and approved by appropriate personnel and the protocols should specify critical steps and acceptance criteria. Typical protocol content would be an:
- Introduction
- Objectives – Description of what validation is trying to achieve and what you’re validating
- The responsibilities of the personnel involved in the validation
- Prerequisites – Activities or procedures that have to happened prior to the validadition excerise
- Production equipment – detailing the equipment necessary
- Test scripts and methods
- Test parameters and acceptance criteria
- Test checksheets – documenting and recording the test results
- Final approval
Once qualification is complete the system, piece of equipment or facility can be released for use to produce pharmaceutical products. So that leads you into the stage which is process validation.
Process Validation Protocol
Process validation is a specific validation activity carried out on manufacturing processes to establish a high degree of assurance that a specific production or manufacturing process will consistently yield a product that meets predetermined specifications and quality characteristics.
A Process Validation Protocol is a documented plan for executing and capturing data from process validation activities.
Typical prerequisites for process validation are that there are:
- Approved standard operation procedures available for the use, control and maintenance of all the systems and processes that are going to be validated
- Critical systems and instruments are calibrated and entered into the calibration program prior to embarking upon process validation
- Critical consistent components must be entered into the site preventive maintenance program prior to starting process validation
- Training requirements must be established for personnel involved in manufacturing operational procedures prior to starting process validation
Key Process Validation Support Documents
Here are some of the key documents that would be reviewed throughout the process of developing a process validation protocol.
- Process development reports or reports where product characterization studies were carried out and technical transfer reports would be key reports to review to design the process validation
- Equipment design requirements and specifications are key documents that will be reviewed
- Operation manuals of the equipment drawings for the equipment schematics etc are also key documents that will be referred to
- Risk assessment and risk analysis documents and reports would be reviewed
- Calibration records of the equipment and instruments that would be used in process validation would be useful documents.
- Standard operating procedures for the equipment and the cleaning would be required
- Training records would be reviewed and these will be the training records typically of the operative staff that would be operating the equipment that the process validation is going to use.
- FAT and SAT documentation for the equipment manufacturer are key parts of the equipment qualification the information in this would also be information that would be useful for to review prior to developing process validation documents.
- Verification protocols of the validation protocols or qualification reports that would be the DQ IQ OQ and PQ and associated data and reports for the equipment
- Process monitoring parameters are also key support documents and these may be part of a batch record or an SOP
- Change management procedure is a further key support document for process validation activities
Document Format
The validation master plan also looks at document format. For each type of validation document, the SOP number which describes the format and the contents should be listed in the plan.
In each SOP the document format and typical content together with approval and document control procedures would be given. Here is an example of a header that would be used in a typical validation document.
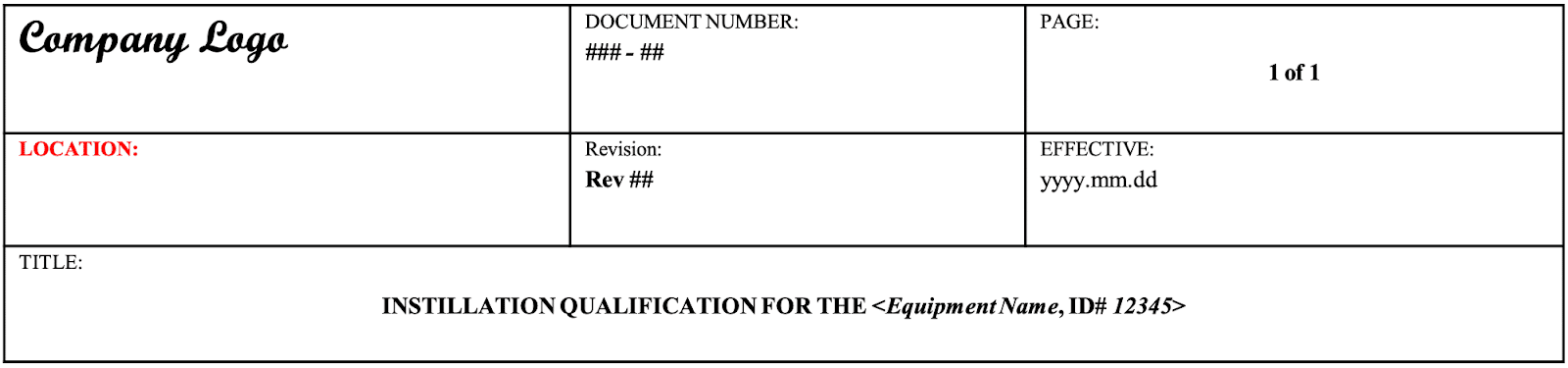
This example here is for an installation qualification.
- The bottom part of the header describes the title of the document in this case it’s an installation qualification and you would insert the equipment name and the equipment ID.
- You would insert the company logo in the header.
- The document would be numbered and there would be an SOP describing the numbering system for documents used in the company.
- Each page of the document should have a page number so the total number of pages would be listed. In this case, if it’s a one-page document it would be page one of one. If it was a hundred pages it would be page one of a hundred and each page would be subsequently listed page two of a hundred, page three of a hundred etc.
- You would indicate the location of the pice of equipment
- You would include the revision number of the document..
- You would include the date (and date format) in which the document was either written or becomes effective from.
6) Develop the validation plan and schedule. Outline resource requirements
You would identify all key validation projects in the Validation Master Plan and outline a completion schedule. You would list the resources assigned to each project together with the responsibilities for each step of the project and the time scale for each project would also be indicated.
7) Define Change Control and Deviation Management Procedures
Validation programs are subject to change control. Each company or organisation should have a procedure describing the change management process.
Change control is a formal process in which changes to equipment systems, procedures, processes, product designs, protocols, etc are proposed by individuals planning to make them in a documented format. Any system, facility, document or process that has the potential to impact product quality and the validated state is subject to this formal change control process.
You would document the reason and justification for the proposed change and submit it for approval. Qualified representatives would review proposed changes and approve them in advance.
You would agree on any additional tests required to make the change in advance of the change. Qualified representatives would review the outcome of this additional testing and the outcome of the change. If the change is approved, it will be documented. Finally, the accepted changes will be communicated to the training department if necessary.
In addition to the statement on change control, you must also address deviations in this section. For example, a typical statement in the validation master plan would be that deviations that occur during validation shall be documented and investigated in accordance with the company’s deviation procedures.
8) Outline Qualification and Validation Strategy, Including Requalification
This section will outline your approach to qualification and your validation strategy.
9) List References to Existing Documents
The validation master plan will list the existing documents it refers to. Typically this would be in some tabular format with a list of the document numbers and the location or the place where these documents can be found indicated.
Conclusion
In summary, a Validation Master Plan is a crucial document that outlines the overall strategy for the validation of a project in a pharmaceutical or medical device company. It helps to ensure that validation activities are planned and executed effectively and that they align with the business objectives of the company.
Further Reading
You might also be interested in reading:
About the Author
Donagh Fitzgerald
Head of Marketing & Product Development
Mechanical/Production Engineer
Donagh looks after the marketing and product development including the training and pedagogical elements of our programs and makes sure that all GetReskilled’s users can have a great online learning experience. Donagh has lived and worked in many countries including Ireland, America, the UK, Singapore, Hong Kong and Japan. Donagh has also served as the Program Manager for the Farmleigh Fellowship based out of Singapore.
Donagh holds Degrees in Production Engineering and Mechanical Engineering from South East Technological University, Ireland.