This course is right for you if:
TU Dublin’s Minimum Entry Requirements:
You must be able to answer “YES” to EACH of the following 4 questions for this “Certificate in eValidation”
- Do you have a sound understanding of GMP rules, regulations and guidelines?
- Can you read engineering documentation such as P&IDs and piping isometrics?
- Do you understand IQ, OQ and PQ?
- Can you populate an IQ OQ PQ Equipment Qualification protocol used in the BioPharma/Medtech Industry?
NOTE:
If you answer “NO” to any of the 4 questions above, you will first need to take our Equipment Validation Training Course (ONLINE) – For Starter Validation Roles and learn commissioning & qualification of equipment and systems and how to populate an IQ OQ PQ Equipment Qualification Protocol. This program covers all the entry requirements above.
What Kind of Roles Would I be Suitable For?
The more validation work experience you have, the better positioned you’ll be to successfully apply for more senior roles upon completion of the program. Here are some of the most common job titles we see advertised and the expected salaries.
Validation Technician
Works as part of the Validation team to measure and analyze the manufacturing process, audit and calibrate equipment and create a document trail that shows the process leads to a consistent result.
Some companies might call this role:
- CQV Specialist
- C&Q Specialist
- Associate QA Validation Specialist
- C&Q Junior Project Manager
- Equipment & Process Validation Specialist
- QA Validation Associate
- QA Validation Specialist
- Validation Specialist
Validation Engineer
Rigorously test and pre-test the systems used to manufacture products and create and document an evidence trail to show that the systems and equipment used, produce a defect-free consistent result. This is a more senior role.
Some companies might call this role:
- CQV Engineer
- Manager / Associate Manager – QA Validation
- QA Validation Engineer
- Quality & Validation Engineer
- Senior Validation Engineer
- Senior Validation Specialist
- Staff Engineer, Quality/Validation
- Validation Scientist
Process Validation Engineer
This is generally considered an advanced role and requires thorough process knowledge and experience with process validation engineers working in engineering design, tech-transfer, upstream and downstream manufacturing. Most practitioners tend to have a lab/science, chemistry or chemical/process engineering background although or have learnt experientially on the job through extensive work experience.
Cleaning Validation Engineer
Design and develop cleaning procedures for new products and manufacturing equipment and also investigate and conduct troubleshooting/root cause analysis of cleaning-related incidents and deviations. This is a highly specialised role so most practitioners tend to have a lab/science, chemistry or chemical/process engineering background or have learnt experientially on the job.
Some companies might call this role:
- Cleaning Validation Specialist
- QA Validation Specialist – Cleaning Validation
- QA Validation – Clean Hold Executor
Your 30-week class schedule
Module 1 – Pharmaceutical Facility Design
In this module, you will receive a strong grounding in the modern pharmaceutical science and engineering concepts of the environmental controls (air) and clean utility systems design that underpins an aseptic manufacturing facility and the quality systems used in this highly regulated environment to ensure the manufacture of safe and effective medicines for the public.
Module 2 – Planning a Validation Strategy
This module will give you a broad understanding of how to develop a Validation Master Plan (VMP) for a typical product lifecycle and to prepare the Process Validation Protocol for presentation during a regulatory audit and meet any regulatory requirements.
Module 3 – From URS to PQ – a Validation Project
This is a workshop driven module where you will develop a P&ID and then back-engineer it into a URS (User Requirement Specification) which will be used to identify the key process measurements that will form the basis of the Performance Qualification (PQ) test script.
Week 21 to 22 – Supplementary Content: Generation of Piping and Instrumentation Diagrams, URS for Hot Detergent and Hot PUW Generation and Distribution Skid System, Equipment List, Instrument List (Incl. both an Attachment and Video Link), Inline Components List (Incl. both an Attachment and Video Link), Piping Line List (Incl. both an Attachment and Video Link), P&ID Instrument Identification (Incl. Video Link Only)
Week 23 – P&IDs
Week 24 – URS Matrix
Week 25 – Workshop
Week 26 – Workshop
Week 27 – Workshop
Week 28 – Workshop
Week 29 – PQ Template
Week 30 – PQ Template
Hear from people who taken this program
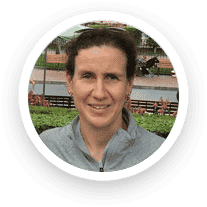
Regina McNamara
“I can Study Around Work and Family Commitments”
I’d recommend this course to anyone that wants to work in the Pharmaceutical and Medical Device Manufacturing industry and is interested in building a successful career in this area. The online experience is working well for me as I study around work and family commitments.
The companies I applied for were very impressed. I am currently working in Boston Scientific manufacturing Balloon Catheters for Gallstone patients.
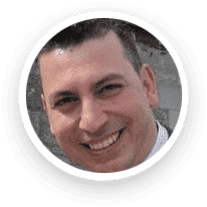
Mehmet Hascan
“Material was Delivered in an Engaging, Interesting and Supportive Way”
Having faced a career change in the middle of an economic downturn, I lost some of myself confidence and needed a major boost. The area of Biopharmaceutical operations and validation was of interest to me as it does play an important role in the pharmaceutical industry at present.
I have now been working at Johnson and Johnson Vision Care as a Validation Engineer and I look forward to putting what I have learned into practice.
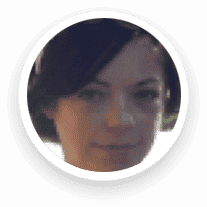
Sharon Egan
“Structurally Well Planned with the Opportunity for Practical Application”
I found the course to be interesting, structurally well planned with the opportunity for practical application of the course modules through various assignments.
I have worked in the Medical device/Pharmaceutical and Food industries and found the course to be extremely relevant to all industries.
Agnes Hove
Domagoj Wunderlich
Patricia Radulescu
Kieran Mac Namara
And delivered by industry experts
Dr. Joe Brady
Full-Time Validation Lead
Lecturer, Technological University Dublin, Ireland
Senior Associate, GetReskilled
Dr. Joe Brady is full-time practicing Validation Lead and an assistant lecturer with Technological University Dublin (TU Dublin), in the School of Chemical and Pharmaceutical Sciences. Joe is a certified trainer and highly experienced in competency-based training. He designs and prepares educational modules and full academic programs ranging from MSc, MEngSc. BSc, to Certificate level, for a range of academic institution.
He is also a supervisor for MSc/MEngSc and PhD theses. Joe has over twenty years of project experience in the pharmaceutical, biopharmaceutical, and medical device industries in Ireland, Singapore, China, The Netherlands, France and the USA.
Professor Anne Greene
Senior Lecturer, Technological University Dublin
Professor Anne Greene is a Senior Lecturer in Pharmaceutical Technology, Validation and Pharmaceutical Quality Assurance to undergraduate and postgraduate students and a Pharmaceutical Projects Manager at Technological University Dublin, Ireland.
In addition, Anne is the Director of the Pharmaceutical Regulatory Science Team and is also secretary of the Parenteral Drug Association (PDA) Secretary, Irish Chapter. Her experience ranges from a technical service chemist, Sterling Wintrop Dungarvan, (now GSK), validation manager at startup Wyeth Newbridge, (now Pfizer) and is a Training Director at NIBIRT in Ireland.
How We Deliver Our Online Courses without ZOOM Classes
With every GetReskilled ONLINE program;
- Centralized Platform: We use one platform (Moodle) where you can log into your classroom anytime. Each week, you’ll watch videos and complete quizzes, tests, interactive activities, and projects. The course materials are available 24/7, so you don’t have to be online at a specific time. There are No Zoom Classes. Study anywhere, anytime, such as after the kids are in bed or on the weekend.
- Flexible Schedule: Your working schedule may be unpredictable, so we offer flexible delivery. You can slow down, speed up, or pause the program as needed.
- Progress Checks: We release one week’s worth of material at a time and manually check your activity logs at the end of each week to ensure you are keeping up with your work.
- Dedicated Course Leader: Your course leader will:
- Help you create a weekly study plan
- Answer any questions
- Check your progress every Monday
- Follow up regularly to support you until the end of the course.
This all helps us to spot any potential issues early and helps you completely finish the program.
Price & Start Dates
Or $799/month for 10 months.
Price Includes:
- End of week progress checks by us to MAKE SURE you finish the program
- Univesity accreditation by Technological University Dublin (TU Dublin), Ireland
- Delivered online so you can learn from home (or anywhere) on your own schedule
- Robust job hunting program that will help you find a job
- Regular & ongoing access to a dedicated career coaching counsellor
No Hidden Fees
- No application fees
- No registration fees
- No resource/book fees
- No graduation fees
- No certificate fees
Please Note: This price is only available to tax residents of Ireland.
Or €299/month for 10 months.
Price Includes:
- End of week progress checks by us to MAKE SURE you finish the program
- Univesity accreditation by Technological University Dublin (TU Dublin), Ireland
- Delivered online so you can learn from home (or anywhere) on your own schedule
- Robust job hunting program that will help you find a job
- Regular & ongoing access to a dedicated career coaching counsellor
No Hidden Fees
- No application fees
- No registration fees
- No resource/book fees
- No graduation fees
- No certificate fees
Or €699/month for 10 months.
Price Includes:
- End of week progress checks by us to MAKE SURE you finish the program
- Univesity accreditation by Technological University Dublin (TU Dublin), Ireland
- Delivered online so you can learn from home (or anywhere) on your own schedule
- Robust job hunting program that will help you find a job
- Regular & ongoing access to a dedicated career coaching counsellor
No Hidden Fees
- No application fees
- No registration fees
- No resource/book fees
- No graduation fees
- No certificate fees
Or £649/month for 10 months.
Price Includes:
- End of week progress checks by us to MAKE SURE you finish the program
- Univesity accreditation by Technological University Dublin (TU Dublin), Ireland
- Delivered online so you can learn from home (or anywhere) on your own schedule
- Robust job hunting program that will help you find a job
- Regular & ongoing access to a dedicated career coaching counsellor
No Hidden Fees
- No application fees
- No registration fees
- No resource/book fees
- No graduation fees
- No certificate fees
Price & Start Dates
Or €699/month for 10 months.
Price Includes:
- End of week progress checks by us to MAKE SURE you finish the program
- Univesity accreditation by Technological University Dublin (TU Dublin), Ireland
- Delivered online so you can learn from home (or anywhere) on your own schedule
- Robust job hunting program that will help you find a job
- Regular & ongoing access to a dedicated career coaching counsellor
No Hidden Fees
- No application fees
- No registration fees
- No resource/book fees
- No graduation fees
- No certificate fees
Please Note: This price is only available to tax residents of Ireland.
Or €299/month for 10 months.
Price Includes:
- End of week progress checks by us to MAKE SURE you finish the program
- Univesity accreditation by Technological University Dublin (TU Dublin), Ireland
- Delivered online so you can learn from home (or anywhere) on your own schedule
- Robust job hunting program that will help you find a job
- Regular & ongoing access to a dedicated career coaching counsellor
No Hidden Fees
- No application fees
- No registration fees
- No resource/book fees
- No graduation fees
- No certificate fees
Or $799/month for 10 months.
Price Includes:
- End of week progress checks by us to MAKE SURE you finish the program
- Univesity accreditation by Technological University Dublin (TU Dublin), Ireland
- Delivered online so you can learn from home (or anywhere) on your own schedule
- Robust job hunting program that will help you find a job
- Regular & ongoing access to a dedicated career coaching counsellor
No Hidden Fees
- No application fees
- No registration fees
- No resource/book fees
- No graduation fees
- No certificate fees
Or £649/month for 10 months.
Price Includes:
- End of week progress checks by us to MAKE SURE you finish the program
- Univesity accreditation by Technological University Dublin (TU Dublin), Ireland
- Delivered online so you can learn from home (or anywhere) on your own schedule
- Robust job hunting program that will help you find a job
- Regular & ongoing access to a dedicated career coaching counsellor
No Hidden Fees
- No application fees
- No registration fees
- No resource/book fees
- No graduation fees
- No certificate fees
Price & Start Dates
Please Note: This price is only available to tax residents of Ireland.
Or €299/month for 10 months.
Price Includes:
- End of week progress checks by us to MAKE SURE you finish the program
- Univesity accreditation by Technological University Dublin (TU Dublin), Ireland
- Delivered online so you can learn from home (or anywhere) on your own schedule
- Robust job hunting program that will help you find a job
- Regular & ongoing access to a dedicated career coaching counsellor
No Hidden Fees
- No application fees
- No registration fees
- No resource/book fees
- No graduation fees
- No certificate fees
Price & Start Dates
Or £649/month for 10 months.
Price Includes:
- End of week progress checks by us to MAKE SURE you finish the program
- Univesity accreditation by Technological University Dublin (TU Dublin), Ireland
- Delivered online so you can learn from home (or anywhere) on your own schedule
- Robust job hunting program that will help you find a job
- Regular & ongoing access to a dedicated career coaching counsellor
No Hidden Fees
- No application fees
- No registration fees
- No resource/book fees
- No graduation fees
- No certificate fees
Please Note: This price is only available to tax residents of Ireland.
Or €299/month for 10 months.
Price Includes:
- End of week progress checks by us to MAKE SURE you finish the program
- Univesity accreditation by Technological University Dublin (TU Dublin), Ireland
- Delivered online so you can learn from home (or anywhere) on your own schedule
- Robust job hunting program that will help you find a job
- Regular & ongoing access to a dedicated career coaching counsellor
No Hidden Fees
- No application fees
- No registration fees
- No resource/book fees
- No graduation fees
- No certificate fees
Or €699/month for 10 months.
Price Includes:
- End of week progress checks by us to MAKE SURE you finish the program
- Univesity accreditation by Technological University Dublin (TU Dublin), Ireland
- Delivered online so you can learn from home (or anywhere) on your own schedule
- Robust job hunting program that will help you find a job
- Regular & ongoing access to a dedicated career coaching counsellor
No Hidden Fees
- No application fees
- No registration fees
- No resource/book fees
- No graduation fees
- No certificate fees
Or $799/month for 10 months.
Price Includes:
- End of week progress checks by us to MAKE SURE you finish the program
- Univesity accreditation by Technological University Dublin (TU Dublin), Ireland
- Delivered online so you can learn from home (or anywhere) on your own schedule
- Robust job hunting program that will help you find a job
- Regular & ongoing access to a dedicated career coaching counsellor
No Hidden Fees
- No application fees
- No registration fees
- No resource/book fees
- No graduation fees
- No certificate fees
Application Deadline: Wednesday 23rd July
Program Starts: 30th July
Start your application
Contact Details For This Course
Geraldine Creaner
11 Frequently Asked Questions
Start your application
Contact Details For This Course
Geraldine Creaner
Got more questions?
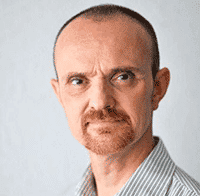
Hi, I’m Donagh Fitzgerald. Chat with me live anytime – just click the blue chat bubble in the bottom-right corner of the page.
I’m online Monday to Friday during working hours (Irish/UK time).
If I’m away from my desk, leave a message and I’ll get back to you as soon as I can.
Or you can fill out the form below and we’ll reply within one working day.