Write a 3,000-word technical report about a new aseptic manufacturing facility
As part of your End of Module Assignment, you will write a 3,000-word technical report to present to senior management about the air, water and steam systems that underpin and support aseptic/sterile processing and cleanroom manufacturing work in a new aseptic pharmaceutical manufacturing plant. The report should cover the 5 key sections:
- Production Logistics
- Process Flow
- Site Master Plan
- Cleanroom Layout
- Utility Support Systems
Your report will help management make critical decisions about the plant design.
Our chemical engineers will review your report and give you written feedback.
Minimum Entry Requirements
This program is highly specialized so you MUST have the following:
Ph.D., Masters, Degree, or Diploma in:
- Mechanical Engineer/Technician
- Maintenance Engineer/Technician
- Facilities Engineer/Technician
- Plant Engineer/Technician
- Production Engineer
- Manufacturing Engineer
- Industrial Engineer
- Graduate Engineer of any of the above
AND YOU MUST
- currently work in the field
OR - have worked or graduated in this field within the last 2 years
If not, check out our University Certificate in eBioPharmaChem
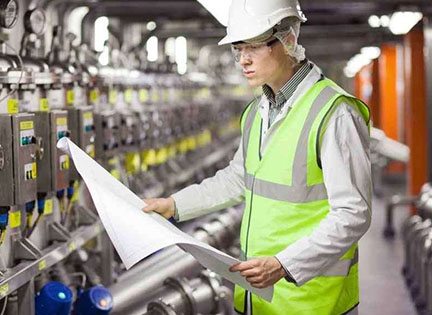
What kind of engineering roles in pharma could I retrain for?
Here are some typical job titles we often see advertised and that you could apply for (depending on your previous experience)
- Maintenance Engineer
- Plant Engineer
- Maintenance Systems Lead – ownership of all preventative and corrective works on plant utilities and equipment.
- Maintenance Planner – the focus is on developing the company asset maintenance program and strategy.
- Lead Utilities Engineer – manage capital projects from inception to delivery and ensure plant availability is maximised.
- Clean Utilities Engineer – ownership of clean utility systems
- Facilities Engineer
- Mechanical Engineering
- Quality/Environmental Engineering
- Manufacturing/Production Engineering (Medical Device Manufacturing or Combination Product Manufacturing)
- Validation Engineering (with our add-on validation program)
I already have an engineering degree. So why take this course?
Your skills are a great foundation for engineering roles within this sector. But you need more..
You need to understand the industry regulations, the different regulatory standards (US, European, World Health Organization, etc), work practices, approaches to risk management, data integrity approaches, and industry protocols that are critical in the manufacture of safe medicines.
You also need to understand how the air, water and steam systems that underpin and support aseptic/sterile processing and cleanroom manufacturing work.
Enroll in this course to learn…
- Introduction – to pharmaceutical, (bio)pharmaceutical manufacturing in a GMP (Good Manufacturing Practice) regulated environment, quality systems vs regulation vs validation
- Industry regulations and guidelines – including, FDA GMPs for the United States, EMA GMPs for European Union, ICH, and PICs GMP regulation
- FDA medical device rules – medical device regulations & guidelines
- GMPs vs ISO 9001:2015 – what’s the difference and why we use both
- Process validation and documentation – design and verification of manufacturing systems
- Supporting technologies – such as purified water generation, storage & distribution, clean steam, water for injection, storage and distribution
- Introduction to quality risk management (QRM) – and the importance of risk management and the basic steps involved in its application
- Key manufacturing technologies – such as organic chemical synthesis, biopharmaceutical manufacturing, tablet manufacturing and aseptic & sterile manufacturing
- Purified water generation – storage and distribution that underpin aseptic/sterile processing
- Clean steam – water for injection, storage and distribution that underpin aseptic/sterile processing.
- Instrumentation process control design – for the generation and distribution of clean utility systems.
- Cleanroom layout design – layout and classification along with the environmental controls pressure profiles
- Aseptic processing – lyophilization and how vials are filled in an aseptic environment
- Quality systems – for cleanrooms for both EMA and FDA guidance on aseptic processing
- Professional writing skills program – This will guide you through the assignment writing process and equip you with the written communication skills you need for working in the industry
You’ll produce a number of deliverables throughout the program including…
- Complete 2 Quality Risk Management workshops on:
- Fault Tree Analysis (FTA)
- Failure Mode Effect Analysis (FMEA)
- Complete 14-question booklets (one for every week’s worth of content) which will summarise what you have learnt for the week and ensure you retain and understand the information.
End of Module Assignments
- Complete a 3,000-word report to give senior management the information they need to make informed decisions about building a new aseptic manufacturing facility.
- Complete a 1,500-word end-of-module written technical report on GMPs.
And take the following skills and knowledge back to work…
- You’ll have a strong foundation in how safe medicines and medical devices are made in a GMP regulated manufacturing environment.
- You’ll understand the air, clean water and steam systems that underpin aseptic/sterile processing.
- You’ll understand cleanroom layout design, layout and classification and the environmental control pressure profiles.
- You’ll have the technical knowledge and understanding of the quality culture necessary to work in this environment.
Hear from people who’ve taken this course
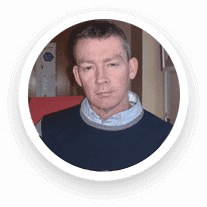
John Ryan
“The course content material is concise and interesting”
“The professionalism and passion of the lecturers comes across in the tutorials which gives the student confidence and encouragement to keep on top of the course. The course content material is concise and interesting. The timing of the release of the lessons is perfect, the student moves at a comfortable pace, one step at a time.”
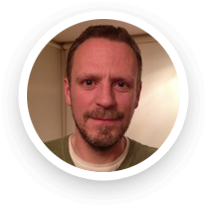
Ronan Balfe
“I would have no hesitation in recommending these courses”
“Studying online gives you the time to do the course in your own time yet with assignment deadlines this made you disciplined to meet the deadlines set. I would have no hesitation in recommending these courses to anyone wishing to gain an education in the pharmaceutical sector.”
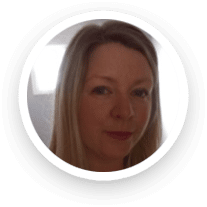
Edel Harkins
“Highly recommended to anyone who has been out of the industry for a period of time”
“I would highly recommend anyone in my situation who has been out of the industry for a period of time to do these courses. They have contributed to my new found confidence in my existing and new qualifications, my improved interview skills and my new job!”
Your 18-Week Class Schedule
Module 1 – Manufacturing Safe Medicines (Weeks 1-5)
Module 2 – Pharmaceutical Facility Design (Weeks 6-18)
This module was developed in consultation with the pharma industry including Pfizer and MSD.
Delivered by an industry expert
Dr. Joe Brady
Full-Time Validation Lead
Lecturer, Technological University Dublin, Ireland
Senior Associate, GetReskilled
Dr. Joe Brady is a full-time practicing Validation Lead and an assistant lecturer with Technological University Dublin (TU Dublin), in the School of Chemical and Pharmaceutical Sciences. Joe is a certified trainer and highly experienced in competency-based training. He designs and prepares educational modules and full academic courses ranging from MSc, MEngSc. BSc, to Certificate level, for a range of academic institution.
He is also a supervisor for MSc/MEngSc and PhD theses. Joe has over twenty years of project experience in the pharmaceutical, biopharmaceutical, and medical device industries in Ireland, Singapore, China, The Netherlands, France, and the USA.
If you’re spending money on an education program, make sure you choose one you’ll finish!
With every GetReskilled ONLINE program;
- We use one centralized platform (Moodle) where you can log into your classroom anytime. Each week, you’ll watch videos and complete a series of quizzes, tests, interactive activities, and projects. The course materials are available 24/7 and nothing requires you to be online at a specific day or time. i.e there are NO ZOOM classes and NO WEBINARS! Study anywhere, anytime, for example after the kids have gone to bed or on the weekend.
- Your working schedules are unpredictable so we offer flexible delivery. Slow down, speed up or pause the delivery of the program.
- We release only one week’s worth of material at a time and then MANUALLY check your activity logs at the end of every week to make sure that you are keeping up with your work.
- You’ll have a dedicated course leader who will email or telephone you if it looks like you’re starting to fall behind. They will work with you to develop a study plan to get you back on schedule and finish the course.
This all helps us to spot any potential issues early and helps you completely finish the program.
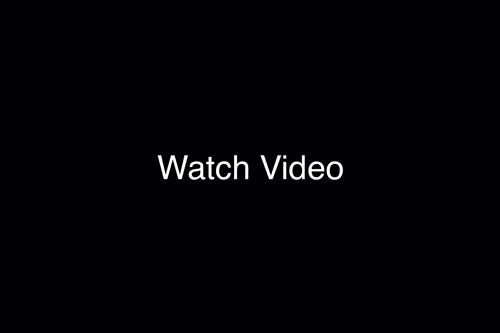
Earn 2 Certificates of Award in:
- The Principles of Pharmaceutical Facility Design
- Manufacturing Safe Medicines and Medical Devices (GMP)
Earn by successfully completing:
- a 3,000-word report to give senior management the information they need to make informed decisions about building a new aseptic manufacturing facility.
- a 1,200-word end-of-module written technical report on cGMPS and passing all assessments.
Add details of your certificates to your CV/Resume or your LinkedIn profile.
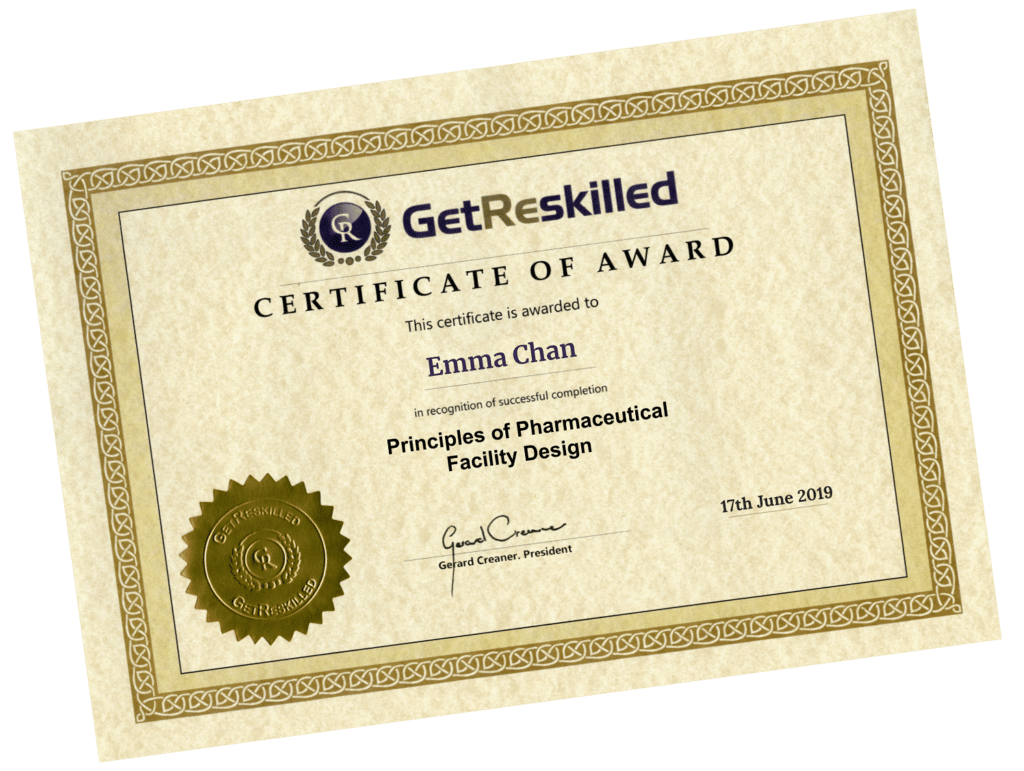
Price & Start Dates
Or $799/month for 5 months.
Price Includes:
- End of week progress checks by us to MAKE SURE you finish the program
- Delivered online so you can learn from home (or anywhere) on your own schedule
- Robust job hunting program that will help you find a job
- Regular & ongoing access to a dedicated career coaching counsellor
No Hidden Fees
- No application fees
- No registration fees
- No resource/book fees
- No certificate fees
18-Day Fast Track Option with Priority Support available for an additional fee.
- Complete this program in 18 days.
- Your course leader will check your progress every morning and follow up with you to keep you on schedule.
- We can start you within 24 working hours upon receipt of payment.
- Contact us to get started.
Or €699/month for 5 months.
Price Includes:
- End of week progress checks by us to MAKE SURE you finish the program
- Delivered online so you can learn from home (or anywhere) on your own schedule
- Robust job hunting program that will help you find a job
- Regular & ongoing access to a dedicated career coaching counsellor
No Hidden Fees
- No application fees
- No registration fees
- No resource/book fees
- No certificate fees
18-Day Fast Track Option with Priority Support available for an additional fee.
- Complete this program in 18 days.
- Your course leader will check your progress every morning and follow up with you to keep you on schedule.
- We can start you within 24 working hours upon receipt of payment.
- Contact us to get started.
Or £649/month for 5 months.
Price Includes:
- End of week progress checks by us to MAKE SURE you finish the program
- Delivered online so you can learn from home (or anywhere) on your own schedule
- Robust job hunting program that will help you find a job
- Regular & ongoing access to a dedicated career coaching counsellor
No Hidden Fees
- No application fees
- No registration fees
- No resource/book fees
- No certificate fees
18-Day Fast Track Option with Priority Support available for an additional fee.
- Complete this program in 18 days.
- Your course leader will check your progress every morning and follow up with you to keep you on schedule.
- We can start you within 24 working hours upon receipt of payment.
- Contact us to get started.
Price & Start Dates
Or €699/month for 5 months.
Price Includes:
- End of week progress checks by us to MAKE SURE you finish the program
- Delivered online so you can learn from home (or anywhere) on your own schedule
- Robust job hunting program that will help you find a job
- Regular & ongoing access to a dedicated career coaching counsellor
No Hidden Fees
- No application fees
- No registration fees
- No resource/book fees
- No certificate fees
18-Day Fast Track Option with Priority Support available for an additional fee.
- Complete this program in 18 days.
- Your course leader will check your progress every morning and follow up with you to keep you on schedule.
- We can start you within 24 working hours upon receipt of payment.
- Contact us to get started.
Or $799/month for 5 months.
Price Includes:
- End of week progress checks by us to MAKE SURE you finish the program
- Delivered online so you can learn from home (or anywhere) on your own schedule
- Robust job hunting program that will help you find a job
- Regular & ongoing access to a dedicated career coaching counsellor
No Hidden Fees
- No application fees
- No registration fees
- No resource/book fees
- No certificate fees
18-Day Fast Track Option with Priority Support available for an additional fee.
- Complete this program in 18 days.
- Your course leader will check your progress every morning and follow up with you to keep you on schedule.
- We can start you within 24 working hours upon receipt of payment.
- Contact us to get started.
Or £649/month for 5 months.
Price Includes:
- End of week progress checks by us to MAKE SURE you finish the program
- Delivered online so you can learn from home (or anywhere) on your own schedule
- Robust job hunting program that will help you find a job
- Regular & ongoing access to a dedicated career coaching counsellor
No Hidden Fees
- No application fees
- No registration fees
- No resource/book fees
- No certificate fees
18-Day Fast Track Option with Priority Support available for an additional fee.
- Complete this program in 18 days.
- Your course leader will check your progress every morning and follow up with you to keep you on schedule.
- We can start you within 24 working hours upon receipt of payment.
- Contact us to get started.
Price & Start Dates
Or £649/month for 5 months.
Price Includes:
- End of week progress checks by us to MAKE SURE you finish the program
- Delivered online so you can learn from home (or anywhere) on your own schedule
- Robust job hunting program that will help you find a job
- Regular & ongoing access to a dedicated career coaching counsellor
No Hidden Fees
- No application fees
- No registration fees
- No resource/book fees
- No certificate fees
18-Day Fast Track Option with Priority Support available for an additional fee.
- Complete this program in 18 days.
- Your course leader will check your progress every morning and follow up with you to keep you on schedule.
- We can start you within 24 working hours upon receipt of payment.
- Contact us to get started.
Or €699/month for 5 months.
Price Includes:
- End of week progress checks by us to MAKE SURE you finish the program
- Delivered online so you can learn from home (or anywhere) on your own schedule
- Robust job hunting program that will help you find a job
- Regular & ongoing access to a dedicated career coaching counsellor
No Hidden Fees
- No application fees
- No registration fees
- No resource/book fees
- No certificate fees
18-Day Fast Track Option with Priority Support available for an additional fee.
- Complete this program in 18 days.
- Your course leader will check your progress every morning and follow up with you to keep you on schedule.
- We can start you within 24 working hours upon receipt of payment.
- Contact us to get started.
Or $799/month for 5 months.
Price Includes:
- End of week progress checks by us to MAKE SURE you finish the program
- Delivered online so you can learn from home (or anywhere) on your own schedule
- Robust job hunting program that will help you find a job
- Regular & ongoing access to a dedicated career coaching counsellor
No Hidden Fees
- No application fees
- No registration fees
- No resource/book fees
- No certificate fees
18-Day Fast Track Option with Priority Support available for an additional fee.
- Complete this program in 18 days.
- Your course leader will check your progress every morning and follow up with you to keep you on schedule.
- We can start you within 24 working hours upon receipt of payment.
- Contact us to get started.
Application Deadline: Wednesday 9th July
Program Starts: 16th July
Start your application
Contact Details For This Course
Geraldine Creaner
Got more questions?
Fill out the form below and we’ll get back to you in one working day.
If you’d like to chat with us quickly, click on the blue chat bubble located in the bottom right corner of the page. We usually respond within a few minutes to a few hours.