Core content developed on a pharma construction project
This program was developed on-site by a team of senior chemical engineers, validation engineers, and biochemists working within an engineering consultancy during the construction of a new pharmaceutical plant to train its own engineers and technicians.
Learn how to fill out a 120-page plus IQ OQ PQ protocol
We will walk you through this step-by-step process and teach you how to populate a blank IQ OQ PQ template to qualify a Clean-in-Place System. The blank template is taken from the construction site of a pharmaceutical plant.
This is a fundamental skill for any validation professional and a key outcome for this program. You will be able to take this completed and substantial document to any job interview and demonstrate your ability to complete this task.
Entry Requirements
You MUST have one of the following:
- You are a process / chemical / petroleum / project / mechanical engineer or a lab/scientist and want to move into validation.
Or - You have commissioning & qualification experience in ANY INDUSTRY e.g. Oil and Gas, Food Manufacturing, Mechanical Construction, etc.
Or - You already work in validation but have no formal training on IQ OQ PQ validation protocols and want to learn more.
Or - You work in a mechanical contracting company carrying out high-purity pipework installations in the pharmaceutical sector.
How will learning qualification protocols help my career?
- Validation Protocols form a fundamental building block of any capital project within this sector.
- Being able to read and interpret a validation protocol is a fundamental skillset of any process, chemical, petroleum, project or any engineer cross-training to work in this area.
- It will boost your qualification for any pharmaceutical companies, engineering consultancies or engineering contractors working on ongoing projects.
- Hit the ground running from day one with this fundamental skillset. Don’t waste months of your time trying to muddle through.
Enroll in this program to learn…
- How to prioritise which parts of the equipment system are critical to validate and which parts are not etc, using component impact assessments and risk management tools.
- How to read/interpret the engineering documentation such as P&IDs, Piping Isometrics & Electrical Loop Drawings used to define the equipment system.
- How the intent of a process (like maintaining the product at the required temperature) is linked to the equipment that will be used to do this.
- The tests along with the functional test scripts necessary to confirm that the installed equipment is fit-for-purpose, i.e. that it will do what it states that it will do based on the User Requirement Specifications).
- How to use a traceability matrix tool to ensure that all requirements defined within the User Requirement Specifications (URS) are tested in the protocol.
- How to qualify equipment, instruments and piping systems, and automation controls.
- How to document all of these steps in validation protocol which you will develop as your end of module assignment.
And
- Complete 2 Quality Risk Management workshops on:
- Fault Tree Analysis (FTA)
- Failure Mode Effect Analysis (FMEA)
- Complete 5 Equipment Validation Protocol workshops on the following to prepare you to populate your own protocol:
- Component Level Impact Assessment
- Equipment Installation Verification
- Piping Installation Verification
- Instrument Installation Verification
- Functional Verification Test
- Complete 12-question booklets (one for every week’s worth of content) which will summarise what you have learnt for the week and ensure you retain and understand the information.
You’ll produce your own 120-page plus IQ OQ PQ qualification protocol to commission and qualify a clean-in-place system
The protocol will detail the following elements;
- Product characteristics – showing what your system is looking to achieve/produce
- Production equipment – detailing the equipment necessary
- Test scripts and methods – telling you the steps involved in conducting a test
- Test parameters and acceptance criteria – defining acceptable test results
- Test checksheets – documenting and recording the test results
- Final approval – documenting that the validation process has been successfully carried out
There are 2 modules in this 15-week program
Module 1 – Manufacturing Safe Medicines and Medical Devices (GMP) (Weeks 1-5)
In this module, you’ll learn about the systems used in pharmaceutical manufacturing. You’ll learn about the rules and regulations such as Good Manufacturing Practices (GMPs) that you need to follow. And you’ll learn enough technical information to get you talking to employers.
Module 2 – Commissioning and Qualification (IQ OQ PQ) of Equipment and Systems (Weeks 6-15)
In this module, you will develop your own 100-page Validation Protocol to commission and qualify a clean-in-place system. You will also learn to read P&IDs, Piping Isometrics & Electrical Loop Drawings used to Develop Validation protocols. And you’ll learn how to qualify equipment, instruments and piping systems, along with automation controls and building facilities.
Already have validation experience?
If you already have some experience working in Validation and know how to populate an IQ OQ PQ validation protocol, check out our academically accredited Pharmaceutical Validation Training Course (Online) – For More Senior Validation, CQV and C&Q Roles.
Hear from people who’ve taken this equipment qualification course
“I can study around work and family commitments”
Studying online is working well for me as I study around work and family commitments.
I would recommend this course to anyone that wants a new career in the Pharmaceutical and Medical Device Manufacturing industry.
“Material was delivered in an engaging, interesting and supportive way”
The administration staff and lecturers at Getreskilled are first class and the course material was delivered in an engaging, interesting and supportive way.
I have now been working at Johnson and Johnson Vision Care as Validation Engineer in Limerick and I look forward to put what I have learned into practice.
“Structurally well planned with the opportunity for practical application”
I found it to be interesting, structurally well planned with the opportunity for practical application of the course modules through various assignments.
I have worked in the Medical Device/Pharmaceutical and Food industries and found the course to be extremely relevant to all industries.
If you’re spending money on an education program, make sure you choose one you’ll finish!
With every GetReskilled ONLINE program;
- We use one centralized platform (Moodle) where you can log into your classroom anytime. Each week, you’ll watch videos and complete a series of quizzes, tests, interactive activities, and projects. The course materials are available 24/7 and nothing requires you to be online at a specific day or time. i.e there are NO ZOOM classes and NO WEBINARS! Study anywhere, anytime, for example after the kids have gone to bed or on the weekend.
- Your working schedules are unpredictable so we offer flexible delivery. Slow down, speed up or pause the delivery of the program.
- We release only one week’s worth of material at a time and then MANUALLY check your activity logs at the end of every week to make sure that you are keeping up with your work.
- You’ll have a dedicated course leader who will email or telephone you if it looks like you’re starting to fall behind. They will work with you to develop a study plan to get you back on schedule and finish the course.
This all helps us to spot any potential issues early and helps you completely finish the program.
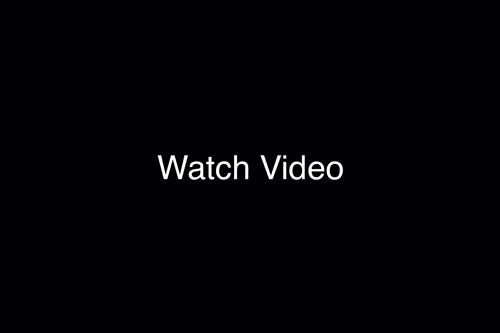
Start your application
Contact Details For This Course
Geraldine Creaner
Hear from people who’ve taken this equipment qualification course
“Validation – A career move to tell your friends about”
“I would say to anybody out there, if you’re thinking about doing this validation course, just go for it. Do it.
There’s a great opportunity within the course to learn. There’s a lot of detail about what goes on in the industry, on the floor, how things happen. Focus just as much on learning to actually educate yourself as much as passing exams. You actually have to embrace it and really get interested in the course material.
“With hard work and determination, you can achieve your goal”
“As a pipefitter/Plumber who worked within the pharmaceutical industry for the last 20yrs, this program gave me the tools I required for a career change and to upskill for a job in pharmaceutical manufacturing. Without this course, I don’t think I would have achieved this. I am happy to say that I have been successful in my employment search.
It is worth the challenge and with hard work and determination, you can achieve your goal.
It gave me a better understanding of pharmaceutical protocols and how the pharmaceutical industry works as a whole.”
Delivered by a Practicing Industry Expert
Dr. Joe Brady
Full-Time Validation Lead
Lecturer, Technological University Dublin, Ireland
Senior Associate, GetReskilled
Dr. Joe Brady is a full-time practicing Validation Lead and an assistant lecturer with Technological University Dublin (TU Dublin), in the School of Chemical and Pharmaceutical Sciences. Joe is a certified trainer and highly experienced in competency-based training. He designs and prepares educational modules and full academic programs ranging from MSc, MEngSc. BSc, to Certificate level, for a range of academic institutions.
He is also a supervisor for MSc/MEngSc and PhD theses. Joe has over twenty years of project experience in the pharmaceutical, biopharmaceutical and medical device industries in Ireland, Singapore, China, The Netherlands, France and the USA.
Your 10 or 15 week class schedule
NOTE: If you worked in a GMP Regulated Pharmaceutical or Medical Device manufacturing environment, you are exempt from the first 5 weeks (Module 1) of the program and get a price reduction.
Module 1 – Manufacturing Safe Medicines and Medical Devices (GMP) (Weeks 1-5)
Module 2 – Commissioning and Qualification (IQ OQ PQ) of Equipment and Systems (Weeks 6-15)
This module was developed in consultation with the pharma industry including Pfizer and MSD.
Earn a Certificate of Award in “Commissioning & Qualification of Equipment and Systems”
Earn by successfully populating a 120-page IQ OQ PQ template to qualify a Clean-in-Place System and get a Certificate of Award in Commissioning & Qualification (IQ OQ PQ) of Equipment and Systems.
Add details of your certificate to your CV/Resume or your LinkedIn profile.
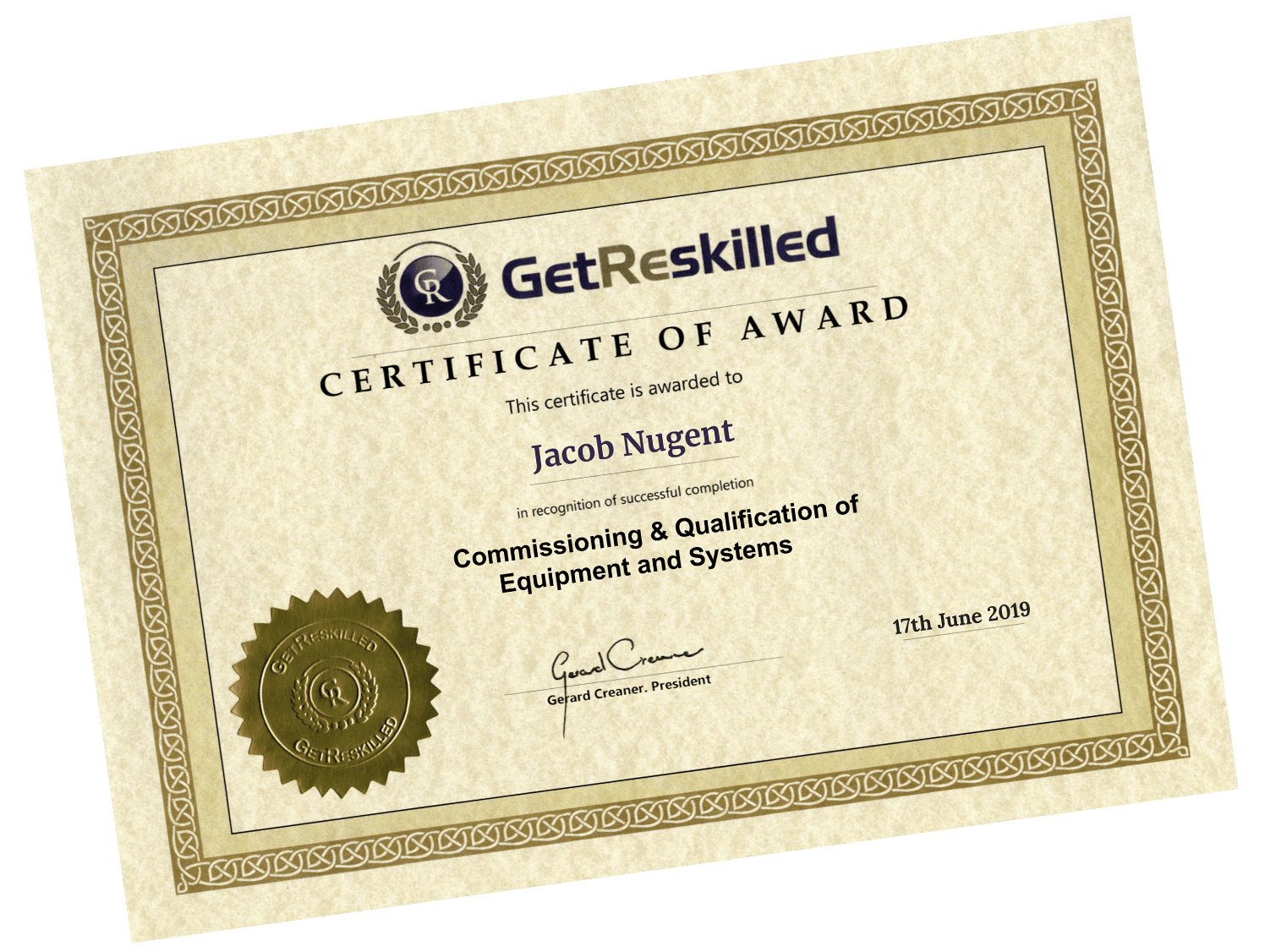
Price
Price for 1-Person
$3,499
Or $799/month for 5 months
Price After Skipping First 5 Weeks. Only available if you’ve GMP Manufacturing Experience
$2,899
Save $600
15 Day Fast Track Option with Priority Support
$3,999
- Complete this program in 15 days.
- Your course leader will check your progress every morning and follow up with you to keep you on schedule.
- START within 24 working hours upon receipt of payment.
Price for 1-Person
€3,199
Or €699/month for 5 months
Price After Skipping First 5 Weeks. Only available if you’ve GMP Manufacturing Experience
€2,699
Save €500
15 Day Fast Track Option with Priority Support
€3,999
- Complete this program in 15 days.
- Your course leader will check your progress every morning and follow up with you to keep you on schedule.
- START within 24 working hours upon receipt of payment.
Price for 1-Person
£2,799
Or £649/month for 5 months
Price After Skipping First 5 Weeks. Only available if you’ve GMP Manufacturing Experience
£2,299
Save £500
15 Day Fast Track Option with Priority Support
£3,499
- Complete this program in 15 days.
- Your course leader will check your progress every morning and follow up with you to keep you on schedule.
- START within 24 working hours upon receipt of payment.
Price
Price for 1-Person
€3,199
Or €699/month for 5 months
Price After Skipping First 5 Weeks. Only available if you’ve GMP Manufacturing Experience
€2,699
Save €500
15 Day Fast Track Option with Priority Support
€3,999
- Complete this program in 15 days.
- Your course leader will check your progress every morning and follow up with you to keep you on schedule.
- START within 24 working hours upon receipt of payment.
Price for 1-Person
$3,499
Or $799/month for 5 months
Price After Skipping First 5 Weeks. Only available if you’ve GMP Manufacturing Experience
$2,899
Save $600
15 Day Fast Track Option with Priority Support
$3,999
- Complete this program in 15 days.
- Your course leader will check your progress every morning and follow up with you to keep you on schedule.
- START within 24 working hours upon receipt of payment.
Price for 1-Person
£2,799
Or £649/month for 5 months
Price After Skipping First 5 Weeks. Only available if you’ve GMP Manufacturing Experience
£2,299
Save £500
15 Day Fast Track Option with Priority Support
£3,499
- Complete this program in 15 days.
- Your course leader will check your progress every morning and follow up with you to keep you on schedule.
- START within 24 working hours upon receipt of payment.
Price
Price for 1-Person
£2,799
Or £649/month for 5 months
Price After Skipping First 5 Weeks. Only available if you’ve GMP Manufacturing Experience
£2,299
Save £500
15 Day Fast Track Option with Priority Support
£3,499
- Complete this program in 15 days.
- Your course leader will check your progress every morning and follow up with you to keep you on schedule.
- START within 24 working hours upon receipt of payment.
Price for 1-Person
€3,199
Or €699/month for 5 months
Price After Skipping First 5 Weeks. Only available if you’ve GMP Manufacturing Experience
€2,699
Save €500
15 Day Fast Track Option with Priority Support
€3,999
- Complete this program in 15 days.
- Your course leader will check your progress every morning and follow up with you to keep you on schedule.
- START within 24 working hours upon receipt of payment.
Price for 1-Person
$3,499
Or $799/month for 5 months
Price After Skipping First 5 Weeks. Only available if you’ve GMP Manufacturing Experience
$2,899
Save $600
15 Day Fast Track Option with Priority Support
$3,999
- Complete this program in 15 days.
- Your course leader will check your progress every morning and follow up with you to keep you on schedule.
- START within 24 working hours upon receipt of payment.
Application Deadline: Wednesday 23rd July
Program Starts: 30th July
Start Your Application
Contact Details For This Course
Geraldine Creaner
Got More Questions?
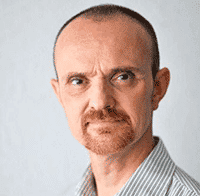
Hi, I’m Donagh Fitzgerald. Chat with me live anytime – just click the blue chat bubble in the bottom-right corner of the page.
I’m online Monday to Friday during working hours (Irish/UK time).
If I’m away from my desk, leave a message and I’ll get back to you as soon as I can.
Or you can fill out the form below and we’ll reply within one working day.